RECRUITMENT
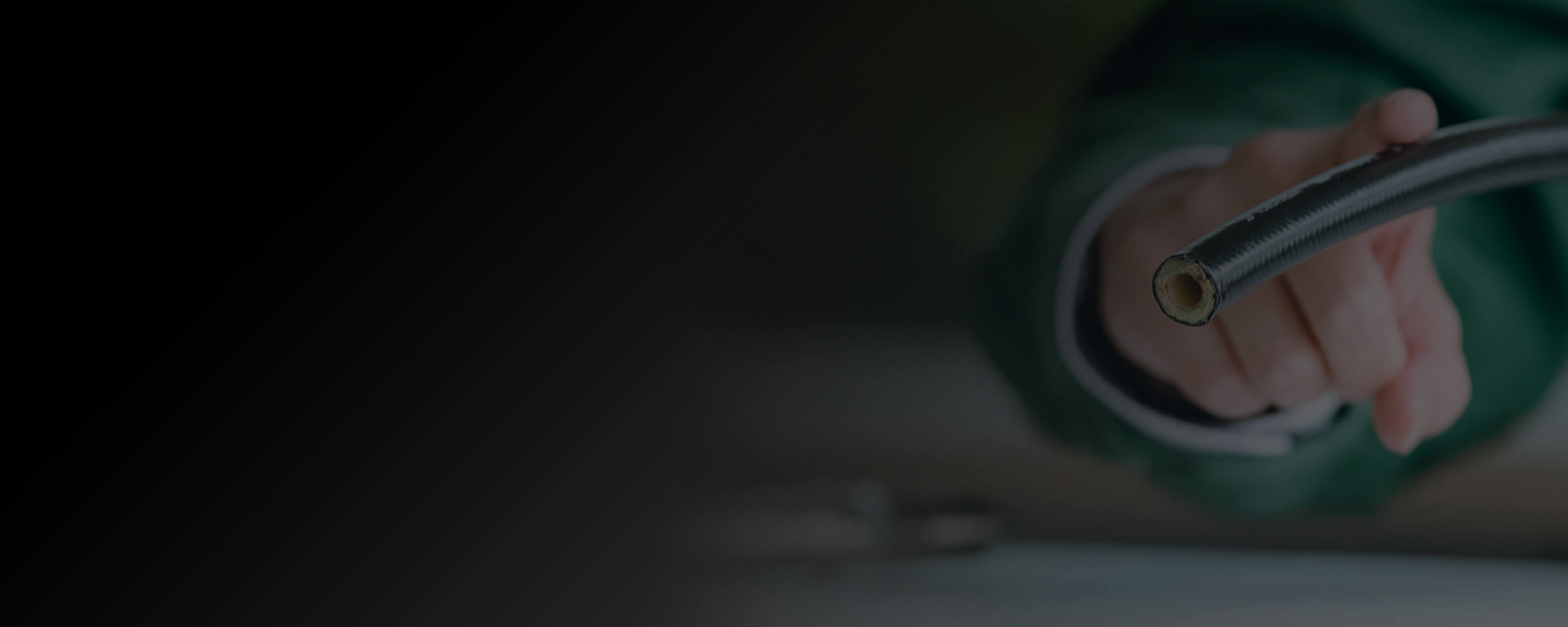
ホースの開発
はじめに
現在、省エネ家電やエコカーを始めとして、エネルギーの化石燃料依存度低減やCO2排出量削減に向けた取り組みが積極的になされている。しかしながら日本に於いては、東日本大震災影響による原子力発電所停止に伴い、電源構成に占める化石燃料の依存度が高まっている。そのエネルギー資源は海外に大きく依存し、新興国のエネルギー需要が拡大しており資源価格の不安定化も懸念されている。
そのような状況の中で、2014年4月、エネルギー政策の基本的な方向性を示すものとして、「エネルギー基本計画(第四次)」が閣議決定された。水素は多様な一次エネルギー源から製造できる上、気体、液体、固体の形態で貯蔵・輸送が可能であり、利用方法次第では高いエネルギー効率、低い環境負荷となることから、将来の二次エネルギーの中心的役割を担うことが期待されている。そのため、この水素を本格的に利活用する「水素社会」の実現に向けた取り組みを加速するとされている(*1)(*2)。実際に、家庭用燃料電池や燃料電池自動車(FCV)を始めとして、小型船舶による燃料電池の実践試験が2016年10月から開始されている等様々な取り組みがなされている。中でも水素・燃料電池戦略ロードマップでは、家庭用燃料電池やFCVを含む次世代自動車の普及・拡大を目指しており、2030年までに家庭用燃料電池は530万台、FCVは80万台程度に普及させるとしている。FCVは2015年12月に一般消費者への販売が本格的に始まり、水素ステーションを含む水素供給インフラの先行整備も進み商用開始が実施された。水素ステーションの設置目標としては、2025年度までに320箇所程度の普及を目指すとされている。また、FCV普及に向け航続距離を伸ばす取り組みも進み、充填する水素ガスの量を増やすことで、700km程度の航続距離が見込めるとも言われている。
横浜ゴムは、水素ステーションで用いる水素ガス充填用ディスペンサーホース(以下水素ホース)を開発している。FCVを普及させるためには、水素ステーションで安全に使用できる水素ホースが必要不可欠で、2003年からNEDO(国立研究開発法人新エネルギー・産業技術総合開発機構)の委託を受け、開発をスタートさせた。流体がガスであるため、水素が材料に対しどの様な影響を与えるか等、材料の耐水素性を評価する基礎検討から始まった。またFCVの航続距離増に伴い水素ガスの充填圧力が上がっている。これまでに充填圧力は35MPa、70MPa、82MPaへと段階的に高圧化しており、現在87.5MPaでの充填に向けたシステム開発等が行われている。これまでに、35MPa用「ibar HG35」、70MPa用「ibar HG70」、82MPa用「ibar HG82」の水素ホースを開発し、それは高圧での耐久性だけでなく軽量かつ柔軟性があるため、充填作業性に優れている。また、水素ホースの開発のみならず信頼性評価法開発にも力を入れている。安全な水素社会実現を目指し、開発した水素ホースの評価を社内に限らず、国内外の試験機関を活用し健全性評価を実施している。様々な耐久試験の他、実機条件を模擬した水素ガスの充填サイクル試験を確立し信頼性評価を実施している。現在、これらの知見を活かし87.5MPa用の水素ホースの開発を行っている。
開発背景
水素ホースの開発は国立研究開発法人新エネルギー・産業技術総合開発機構(NEDO)からの委託により、一般社団法人水素供給利用技術協会(HySUT)、九州大学、日本合成化学工業株式会社と連携し、水素環境下での材料評価や耐水素性材料の開発を実施している。横浜ゴムは、最終製品となるホースの設計開発を担っている。
FCVの普及には、水素ステーションの普及とその航続可能距離が一般ガソリン車同程度であることが求められる。特に航続距離を増加させるためには、より多くの水素ガスをFCVのタンクへ充填する必要があり、言い換えればより高い圧力で充填することが求められる。その結果、充填時間に関しては約3分程度と一般ガソリン車とほとんど変わらないレベルで充填が完了できるがその一方、より高い圧力で水素ガスを充填するためには、断熱圧縮を考慮して、水素ガスを事前に冷却する(プレクール)必要がある。結果的に水素ガスの温度は-40℃~-33℃の間で冷却され、FCVへ充填される。従って、水素ホースは、高圧かつ低温の水素ガスに繰返し耐えなければならず加えて、水素は分子サイズが特に小さいことからホースに用いる各材料のガス透過性、耐ブリスタ性といった耐水素性も開発の重要なファクターとなる。
また、開発した水素ホースの健全性を確かめることが重要になる。特に、ホース開発は、周辺機器やステーションシステムの開発と並行して進めているため規格やユーザー要求が明確でない。従って、製品を開発しながら評価する「試験方法そのもの」を評価していく必要がある。
試験の一例として、耐圧力性能を確かめるため、約400MPaもの超高圧を負荷した耐圧試験や、油や水素ガス流体での耐久性評価のための繰返し衝撃圧力試験(以下インパルス試験)などを実施している。油圧のインパルス試験は一般的な評価方法として知られているが、特に水素ガスインパルス試験はその実施自体が初めてのため、細かな設備・温度・圧力条件等の試験条件の適正化検討も必要であった。この結果、油では見られない水素特有の現象を検出するなど水素ホース開発に必要な様々なデータを蓄積している。また、実施した試験については関係機関と連携し、国際標準(ISO)や国内自主基準(JPEC-S)の制定も目指している。
横浜ゴムの水素ホース
表1に水素ホース仕様を示す。内外面層に樹脂、補強材には高強度繊維補強材や鋼線ワイヤが使用されている。内面には水素ガス透過性(透過のし難さ)と可撓性を両立する樹脂材料を採用し、超高圧に耐えうる高強度繊維補強材を補強材に用いている。更にHG82は耐久性向上のため補強層最外層に鋼線ワイヤを有することが特徴である。
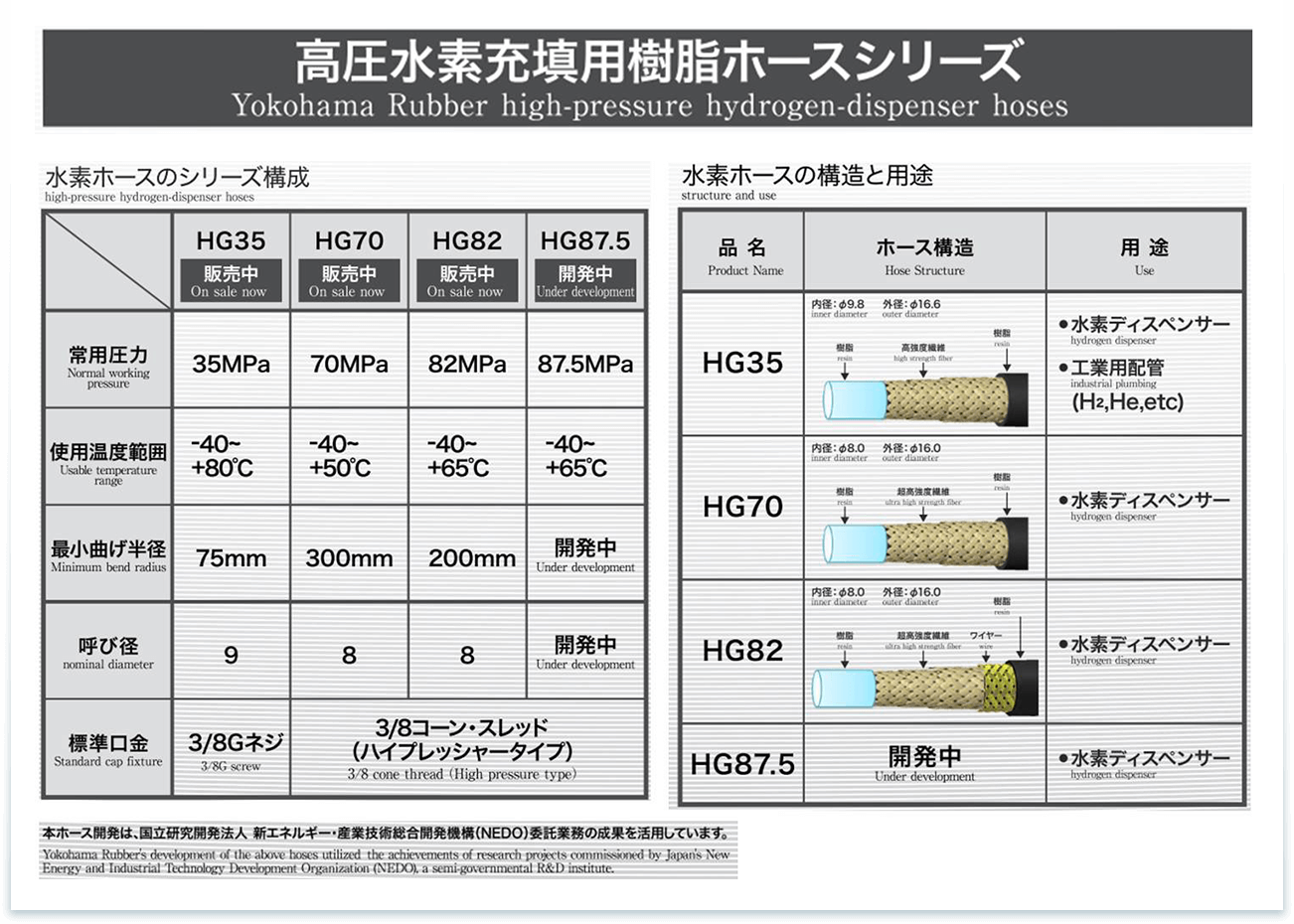
ibar HG82ホースの開発背景
各水素ホースの流体は水素ガスであるが、35MPa用はプレクールが無く常温の水素ガスが充填される一方で、70MPa以上では断熱圧縮を考慮してプレクールが有り、その温度は-40~-33℃に冷却されている。表2にHG70と今回新規開発したHG82での開発目標を示す。両者の大きな差は、使用圧力(耐圧性能)と使用回数(耐久性)にある。使用圧力こそ12MPa程度の差ではあるが、ホース製品の耐圧性能(設計圧力の4倍)は約80MPa以上も向上させる必要がある。その上、水素ガスでの衝撃繰返し耐久試験(以下水素IMP試験)の目標値もFCVの普及ステップの各目標値への対応に伴い810回から6,600回※へと引き上げられた(※6,600回とは、1年間ノーメンテナンスで使用するため1日に6台のFCVが水素ステーションへ充填に来ることを想定し、3倍の安全率を掛けた業界目標値)。従って、HG82ホースの開発は、従来ホースに対して①耐圧性能②耐久性能を高いレベルで実現する必要があった。また、開発したホースの健全性評価法についても検討実施している。特に耐久性評価では、油圧や水素ガスを用いたインパルス試験の他に、水素ステーションの実機条件を再現した模擬実証試験を実施している。
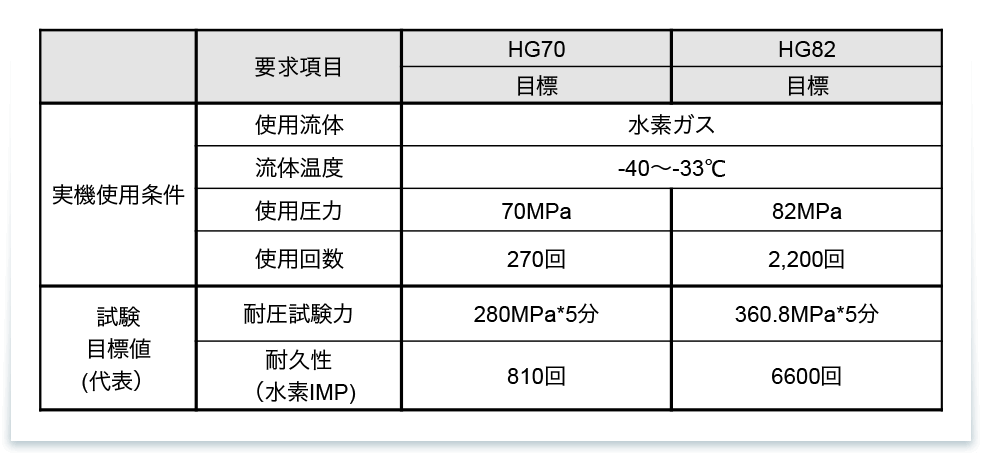
開発課題:耐圧性能
ホースは、流体の圧力によって発生する軸方向の力と周方向の力を施工された補強材によって支えている。そのため、補強材自体の強度が高いほどその耐圧性能を向上させることができる。その一方で、一般的に補強材の剛性が高くなるためホースが硬くなり(曲げにくくなり)、更に重量が重くなることで充填時の作業性が悪化する懸念がある(充填ホースの開発当初、金属フレキ管が採用されていたが、作業性の悪さが課題となっていた)。そのため横浜ゴムでは、超高強度の繊維材料を用いることで昇圧化対応するとともに柔軟かつ軽量な充填ホースを実現している。HG82ホースでは要求される耐圧性能を満足させるため、従来品に対して編組構造の最適化を実施し360.8MPa(5分間)の耐圧を満足させた。
開発課題:高寿命化にむけて
HG82ホースは高圧でかつ低温の水素ガスが流体として使用されるため、内圧による繰返し応力が内面樹脂、補強材へ負荷される。
そこで先ず、補強層構造の耐久性評価のため高低温の油圧によるインパルス試験を実施した。内圧による力の伝播バランスが整っていないと補強層の一部分に負荷がかかるため、疲労破断する恐れがある。開発したHG82ホースは、補強層構造の最適化設計を行うことで-40℃と+65℃の温度条件でかつ設計圧力以上の負荷(96.3MPa)に於いて、疲労破断等の異常が無く走行し、補強層構造の耐久性を確認している。
内面樹脂の耐久性評価については、これまでに九州大学と共同で実施した樹脂材料の耐水素性の評価実験において、低温の高圧水素ガス環境下で樹脂に歪(応力)を与えると、水素が作用しソルベントクラックが発生することを明らかにしてきた。従って高寿命化を実現するためには内圧によって発生する内面樹脂の歪を抑制することが必要となる。HG82ホースは補強層構造に鋼線ワイヤ層を設けることによって、内圧によるホースの膨張の更なる抑制を実現している。同ホースを、-40℃~-33℃の水素ガスを流体として行う水素インパルスを実施し、開発目標を満足する耐久性を有することを確認している。またこの様なインパルス試験の他、模擬実証試験を実施している。模擬実証試験とは、ホースの取付状態、温度、充填圧力等の試験パラメータを実際の水素ステーションに近い条件に再現し信頼性を評価する横浜ゴム独自の試験である。これにより実環境下に近い形で様々なデータを取得し各水素ホースの耐久性評価を行い健全性の確認をしている。また、模擬実証試験の結果と他の試験結果と比較することで各試験のシビアリティを算出でき、短期間で耐久性評価ができる促進試験の開発などにも役立つ可能性もある。
今後の課題
FCVや水素ステーションの普及に向けて、今後更なる昇圧化と耐久性向上への対応が必要となる。そのためには、耐圧効率を向上すべく補強層材の選定、補強層構造の開発や樹脂の歪を抑制させる構造設計が必要である。また、耐久性向上を目指して樹脂材料の耐水素性を向上すべく、材料開発とその評価が必要である。
各試験方法の妥当性評価や実機での寿命推定手法を確立するため、各試験及び実機で発生する樹脂の残留歪について光弾性法を用いた応力分布の解析技術を確立し、定量評価していくことが課題である。
参考文献・資料
- *1:エネルギー基本計画(平成26年4月)
- *2:NEDO水素エネルギー白書