Products
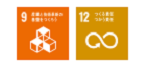
Aiming to realize a new level of comfort in tires, by accumulating technologies, and supporting the mobility society and social infrastructure of the future.
Strengthen information services by digitizing tires in response to the "automation" and "electrification" of automobiles, and pursue environmental and safety technologies.
Click here for PDF version.
Strengthen information services by digitizing tires in response to the "automation" and "electrification" of automobiles, and pursue environmental and safety technologies.
Consumer Issues
Management |
---|
Customer Health and Safety |
---|
Marketing and Labeling |
---|