Kameyama Bead Company, Limited
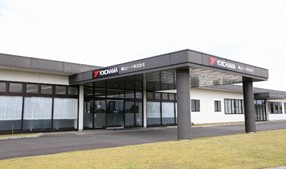
Production and sales of beads for tires
Total site area62,457m2
Number of employees155 (as of March 2023)
Location820-6, Taiokadera-cho, Kameyama city, Mie 519-0168, JAPAN
Contact for consultation and complaintsTel: +81-595-83-1102 Fax: +81-595-83-1082
Message from the President
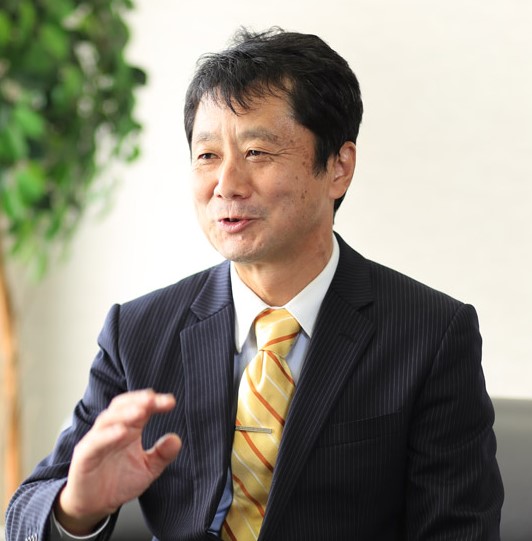
Hirofumi Imamura
In January 2015, our company started a new path as a specialized manufacturer of bead wires for tires, wholly owned by Yokohama Rubber Co.
Our company is located in a corner of Meihan Kameyama-Seki Plant Complex in Kameyama City, known for Kameyama-juku and Seki-juku on the Tokaido-way.
We manufacture and sell bead wires, the main parts of tires, to Yokohama Rubber's tire production bases in Japan.
We hope to support Yokohama Tire by manufacturing safe, high-quality, and high-performance products using the advanced technology we have cultivated since our establishment.
With "Challenge, Fair, Open" as our action guideline, we are working every day to become a company where employees themselves act as parts manufacturers that maintain the quality of Yokohama Tire and continue to take on new challenges as one.
Organizational Governance
- Create a corporate culture that greets employees, observes rules, and does not leave or allow abnormalities to occur.
- All employees have a sense of professionalism, identify waste individually, and work together to make improvements.
- Continuously provide reliability through comprehensive manufacturing capabilities specialized in beads.
Mid-term Policy
- Establish a system to provide products of the required quality at the appropriate time.
- Clarify the roles of equipment and personnel, and promote technological development and on-site improvements that do not rely solely on personnel.
- Further improve the work environment (safety, disaster prevention, light labor) to create a diverse workplace.
- Create a production system that is resilient to rapid changes in the environment (quantity and workforce).
- Create an attractive corporate organization with high employee satisfaction (ES).
Action Guidelines
Challenge: Never be satisfied with the status quo, never give up, and take on challenges with faith.
Fair: Follow the rules, accept diverse work styles, and do what needs to be done.
Open :Do not take matters into your own hands, share information among all employees, and cooperate with each other.
Compliance Policy
We distribute "Compliance Cards" to all employees to ensure that compliance is thoroughly implemented, and have set up a compliance consultation counter and suggestion boxes, aiming for organizational management with a high level of self-cleansing function.
Compliance Education
The Compliance Committee meets once a month and conducts compliance education to raise employee awareness.
Human Rights
Employment of People with Disabilities
The number of employees with disabilities in FY2022 was 4 (the legally mandated number of employees is 3), maintaining a high level.
We will continue our efforts to employ people with disabilities and enhance the workplace environment.
Diversity Promotion
Since 2020, we have held a luncheon for women working in the company on International Women's Day, March 8 every year to promote women's activities.
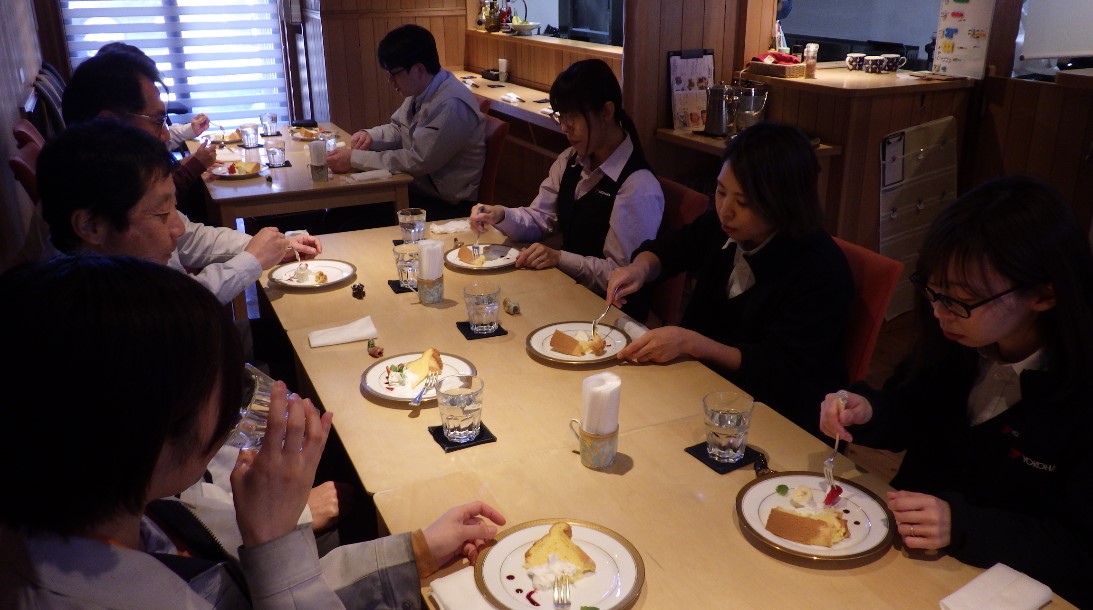
Outside meal on International Women's Day, March 7, 2023
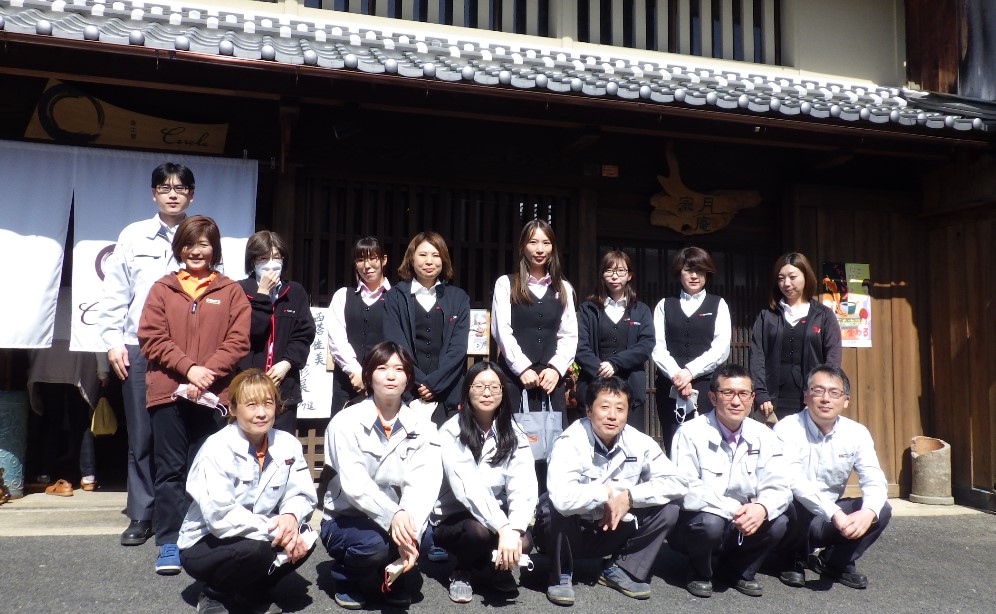
Outside meal on International Women's Day, March 8, 2022
Labor Practices
- Prioritize safety and health above all else, and work to improve safety and health activities with the participation of all employees.
- Implement safety and health activities in an organized manner and practice continuous improvement by repeating the PDCA cycle.
- Promote the creation of a comfortable work environment where employees can work with peace of mind, and work to improve mental and physical health.
- Raise awareness of the importance of health and safety among workers and provide necessary education and training.
Priority safety issues
Deployment of safety model and promotion of reducing workload, development of BCP system and promotion of earthquake countermeasures
- Continue to achieve no accidents (lost time, lost workdays, traffic accidents, small fires)
- Create an easy-to-work-in workplace by developing a safety model, improving the workplace environment, and reducing workload
・Identification and reaping of risks through risk assessment and Hiyari-Hatto activities
・ Improvement of safety sensitivity through KYT activities and open work observation - Build BCP foundation and promote earthquake countermeasures
Health and safety activities
Safety and health committee meetings and safety patrols are held once a month to check for hazardous areas in the plant.
In addition, we strive to identify and eliminate risks that may lurk in daily operations by attending KYT classes outside the company, conducting risk assessment activities, and submitting near-miss reports, thereby creating a safe working environment.
Disaster Response
We focus on disaster drills such as in-house evacuation drills (twice a year, including one night drill) and safety confirmation drills using an app (four times a year).
We also participate in disaster drills in cooperation with Yokohama Rubber to identify problems and make improvements.
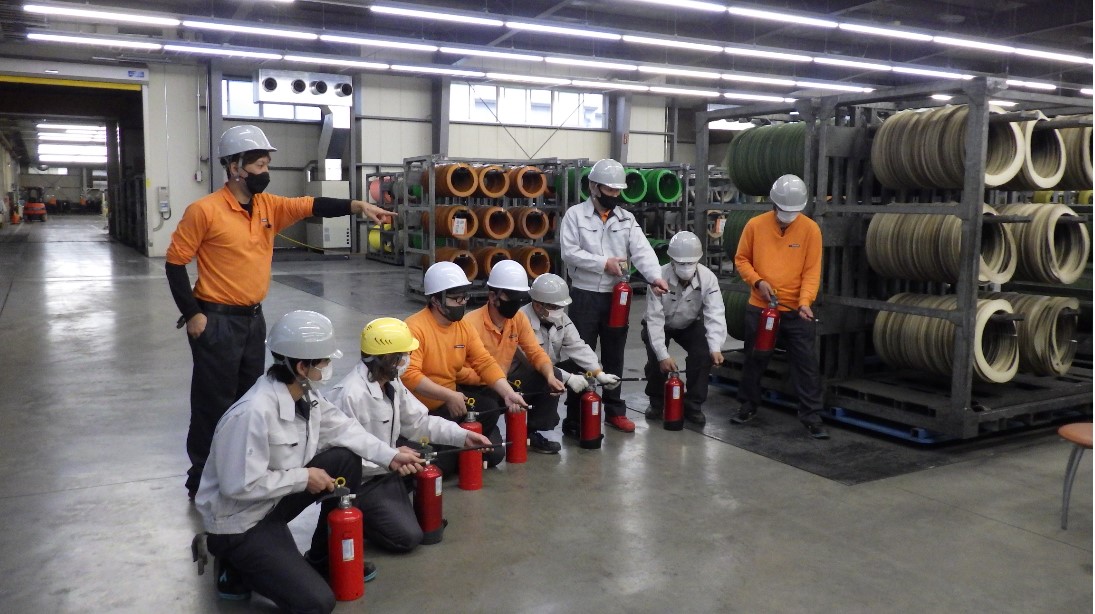
Evacuation drill on November 24, 2022
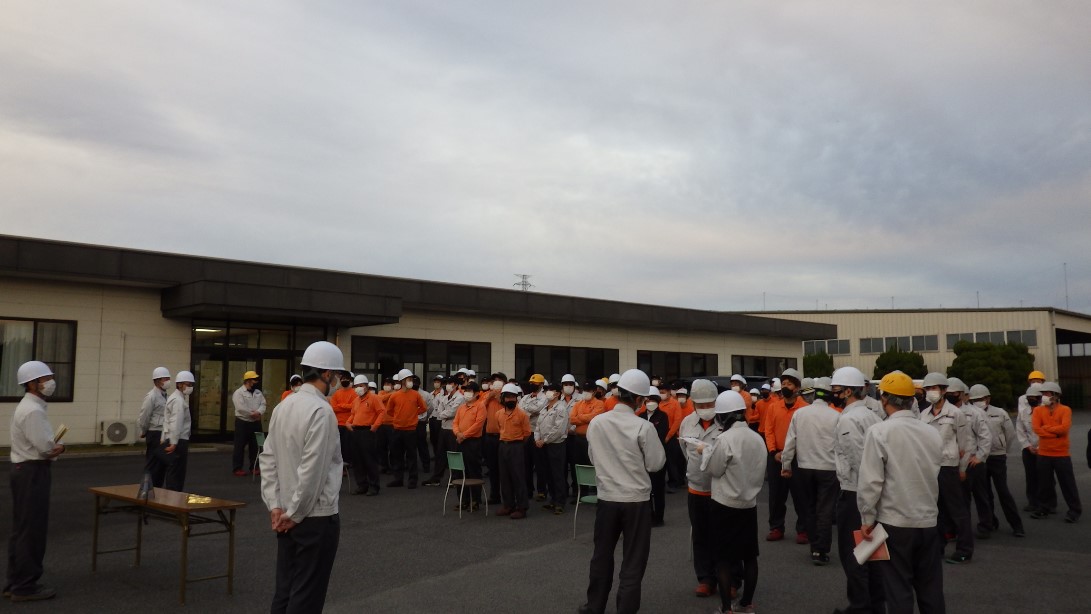
Evacuation drill on November 24, 2022
Recruitment Efforts
We are developing recruitment activities mainly through job sites, and starting to use the job site Indeed.
In addition to regular hiring of new graduates, we are also actively recruiting permanent mid-career employees.
Employee Education and Training
We provide education materials on compliance, environment, safety, and quality to all employees.
We also actively utilize external training programs, such as managers' training and KYT training, to promote employee education and training.
We have recently established a new qualification allowance system to encourage employees to work positively toward acquiring qualifications.
Creating a workplace where people can take on challenges
We encourage our employees to take on challenges without fear of failure, and we are working to improve even the smallest matters through our improvement proposal forms.
Promotion of Employee Health
A new health promotion allowance (allowance for no smoking on company premises) was established to promote a better understanding of one's own health and to encourage the practice of health promotion.(Smoking rate as of April 1, 2022: 27%)
Promotion of Diversity
- We have introduced a teleworking system to allow a variety of work styles and meet the needs of our employees.
- We are also promoting the hiring of female employees at production sites to create a more diverse workplace.
The Environment
- To implement environmentally friendly measures in all of our activities in accordance with Yokohama Rubber's policies.
- Operate an environmental management system and continuously engage in environmental improvement activities.
- Promote energy-saving activities, resource conservation, and resource recycling to realize a carbon-neutral, recycling-oriented society.
Priority Environmental Issues
Cost reduction through 3R model deployment and GHG emission reduction through energy saving improvement deployment.
- Continue to achieve zero emissions
- Reduction of disposal costs by strengthening 3R activities
・Reduction of product scrap and improvement of rework/reprocessing ratio in conjunction with quality improvement activities
・Improvement of the purchase ratio of valuable resources by sorting waste materials - Promote energy conservation by reducing energy loss and adopting high-efficiency equipment
Acquisition of ISO 14001 certification
We acquired ISO14001 certification in July 2020.
We aim to become an environmentally friendly company by increasing our sensitivity to environmental burdens and risks.
Initiatives for Environmental Issues
- We continue to achieve zero emissions by recycling all industrial waste.
- We are promoting recycling of waste by using rubber and wire separation equipment. We are working to reduce waste by strengthening 3R activities, such as reducing waste by welding wire ends to reduce product scrap.
- To reduce the use of organic solvents (rubber solvents), we have changed the bonding method for TBS filler splices from the spraying method to the heating method. We are also studying the possibility of changing the treatment method for TBG insulation pretreatment, and have begun tests.
- Introduced intermittent operation control system for factory air conditioners to save energy.
Environmental data
Move the screen to the left or right to see the table information
Category | FY2018 | FY2019 | FY2020 | FY2021 | FY2022 |
---|---|---|---|---|---|
Waste disposed (t) | 70 | 82 | 75 | 61 | 83 |
Proportion sent to landfill (%) | 24.29 | 82.93 | 28.00 | 0.00 | 0.00 |
Water usage (m3) | ― | ― | ― | 8,132 | 9,328 |
Greenhouse gas emissions (1,000t-CO2) | ― | ― | ― | 3,337 | 3,677 |
Fair Operating Practices
We conclude basic transaction agreements with our business partners and establish fair relationships with them in compliance with laws and regulations.
Directors and employees also comply with laws, regulations, and internal rules, and strive to conduct proper corporate management and business operations.
Consumer Issues
- Operate a quality management system and engage in continuous quality improvement activities.
- Aim for "zero leakage of abnormal quality products outside the company" through activities that get to the root cause and dig deeper into the facts.
Priority Quality Issues
Expansion of quality sensors and restructuring of the system for guaranteeing own process/preventing leakage outside the company.
- Establishment of processing conditions that prevent defects from occurring
・Analysis of true causes of abnormalities and establishment of (tentative) standards to prevent recurrence - Further clarification of quality control items
・Early detection of abnormalities through constant monitoring and trend management
・Development and horizontal deployment of quality sensors - Review of quality education system
・Expansion of competence certification system (quality dojo, inspector certification system)
Community Involvement and Development
Encourage participation in volunteer activities
We provide employees with opportunities to voluntarily contribute to society by establishing a new volunteer leave program.
We encourage employees to contribute to various social issues such as local welfare, environmental protection, and educational support.