Suzhou Yokohama Tire Co., Ltd. (CSZY)
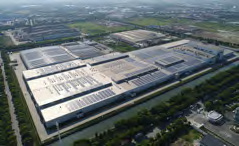
Production and sale of tires for passenger cars
Total site area201,500 m2
Number of employees830 (as of the end of December 2022)
LocationNo.158, Huaqiao Road, Xuguan Industrial Park, Suzhou National New & Hi-Tech Industrial Development Zone Suzhou, Jiangsu Province, 215151, China
Contact for consultation and complaintsTel: +86-512-6818-1008 Fax: +86-512-6818-1007
E-mail: xuejingyi @cszy.yokohamatire.com
Message from the President
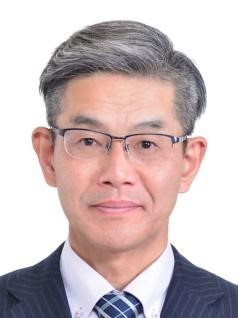
Tomoyuki Okuno
Suzhou is famous for its rice, tea and freshwater crabs, known as Shanghai crabs in Japan, as well as its abundance of fish. Thus, many people from Japan also come here on sightseeing tours.
The plant began operations in 2008 as a truck and bus tire plant and added passenger car tire production in 2014. The plant, which completed production of truck and bus tires at TB plant in 2017 and was renovated to produce passenger car tires, began production in October 2019, and on October 12, 2019, the opening ceremony and the "Forever Forest" tree planting activity were held simultaneously. In addition, by November 2019, the plant will have achieved 10 million passenger car tires, and is expected to have an annual capacity of 4.26 million tires by 2022, including the renovated plant, as it continues to enhance its presence as a passenger car tire production base in China.
Our goal is to be a company that coexists in harmony with the local community by engaging in activities that contribute to the local community and take root in the community in this rich land. On the other hand, due to its affluent location, it is highly sensitive to the environment and its regulations are much higher than Japan's. Environmental measures for odors and VOCs are required at a high level. In addition, we will continue to participate in the release of fry into the lake, continue our tree planting activities in the Forever Forest, and promote biodiversity activities in the region.
Through our health and safety activities, we will help our employees feel that their safety is a family's happiness, and all of us will strive to become a company that is admired and trusted by everyone to achieve the goal of "becoming a “company that is attractive to both employees and regional communities.”
Organizational Governance
A Code of Conduct has been drawn up, which is printed on a card (together with the company’s policy) and distributed to all employees.
Workplace communication
Within the company, corporate decision-making is conducted through the holding of key meetings (including management meetings, cost meetings, safety meetings, environmental meetings, quality meetings, meetings of the human resources committee, minister's meeting, section chief's meeting, general manager's meeting, field morning meeting and CSR education) on a periodic basis.
Human Rights
CSR education
All employees receive compliance training twice a year. Internal control-related education is provided for internal control team members. We publish a quarterly CSR plant magazine to disseminate knowledge on the subject.This year, we added legal education for specialized operations: for example, education on contract risk management, targeting purchasing and finance.
We invited outside lawyers to conduct job crime education for personnel at the elementary engineering master level and above in order to ensure that everyone is upholding the law.
CSR training has been conducted once/month for managers at the section manager level and above, as well as for worker representatives.
Grievance resolution
Based on the feedback from the government's environmental department, we are not only complying with emission control standards but also reducing the burden on the local community by improving environmental facilities while taking into consideration the local residents.
In response to government environmental audits, we are also continuously promoting improvement activities.
We have developed environmental facility management standards and standard operating procedures to improve our management capabilities.
We are also reducing our impact on the surrounding environment.
Labor Practices
Building a safe, healthy workplace environment
Slogan: Personal safety, family happiness (my safety is my family’s happiness)
We also passed an external audit for ISO 45001.
Improvements have been made to prevent serious accidents involving large rolls in 2022. All 12 units in total have been improved.
Improvement of on-site noise was implemented in 2022. Brake noise was improved for single bead winding. All 5 units at the second plant have been improved. Others are also being developed as planned.
- In FY2022, 92 new work standard documents were created and 342 were reviewed. In FY2022, 50 new Fault Handling Procedures documents were created and 47 were reviewed.
- Open work observations were conducted 12 times. Internal work training was conducted 47 times.
- The deployment of internal occupational accidents and those at other plants totaled 173 cases, and 140 measures were implemented.
- Risks increased to 7 cases of Level V, 9 cases of Level IV, 97 cases of Level III. 6 cases of Ⅴ level, 7 cases of Ⅳ level, and 49 cases of Ⅲ level were improved.
- To strengthen management of subcontractors, we conducted training for contractors three times (total of 129). We awarded a certificate of qualification for construction safety supervisor from our company.
We are improving the level of safety management through the continuous implementation of initiatives such as KYT, near-miss submissions, one-on-one education, periodic risk assessment, work observation and training, and review of work standards.
Labor safety and health
In accordance with China's national regulations, all employees who join, are enrolled in, or leave the company undergo occupational disease medical examinations, as well as workplace environment measurements and heat stroke training.
There will be no outbreak of occupational diseases in FY2022.
Labor relations
The company holds regular meetings with the labor union for the exchange of views.
We were awarded as an excellent company in Suzhou labor-management relations in 2021.
Human resources development and training
- Three-level safety training (plant/department/process level) is conducted for new employees, to certify them to work alone.
- Improved the level of KY implementation in key sections (pilot program in the Maintenance Section).
- In safety education, occupational disease risks were educated to occupational health staff in each division.
- Safety training for all employees is conducted at the general manager's morning meeting in March, June, and October.
- Safety training for section managers to general managers was conducted. (2 times/year).
- Special fire prevention training was conducted. (For all employees. Safety personnel from outside contractors and resident contractor personnel also received training.)
Responses in case of disaster
We have an emergency contact system and first aid plan for safety incidents. In the event of a disaster, the emergency contact system is used to report to the general manager.
The first aid plan is immediately activated to deal with the disaster.
Each section conducts first aid drills. The contents of these drills include falling from a height, getting caught in a vehicle, collision with a towing vehicle, chemical leakage, etc. A total of 49 drills have been conducted.
In 2022, evacuation drills against fire were conducted 6 times and fire drills were conducted 4 times.
Firefighting drills were conducted for resident subcontractor personnel, including security guards, cafeteria staff, and cleaning staff.
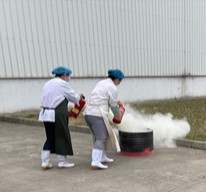
Firefighting drills for resident subcontractor personnel
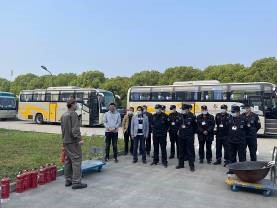
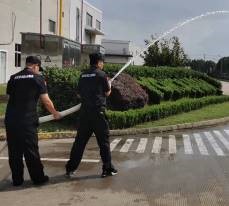
Firefighting drills for resident subcontractor personnel
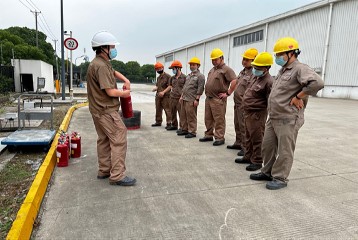
Firefighting training by volunteer firefighters
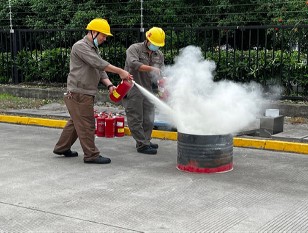
Firefighting training by volunteer firefighters
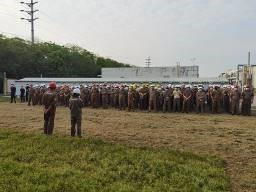
Evacuation training (daytime and nighttime)
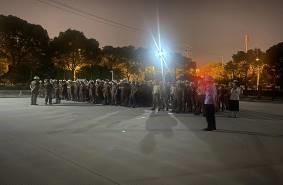
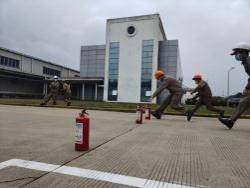
Fire Drill Contest
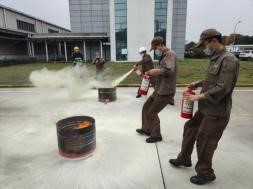
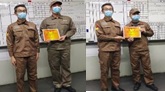
Fire Drill Contest
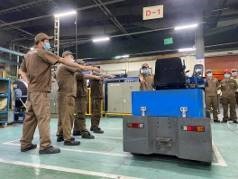
KY (hazard prediction) training, KY contest
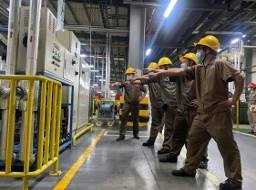
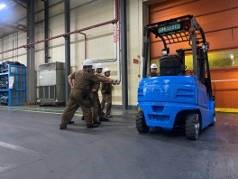
KY (hazard prediction) training, KY contest
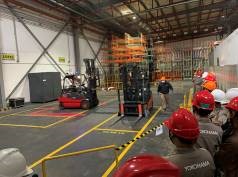
Open work observation
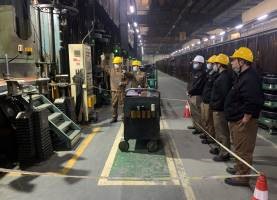
In-department work observation
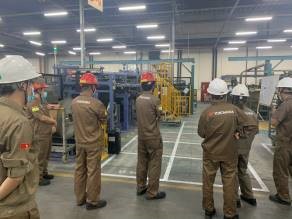
Safety observation of new equipment
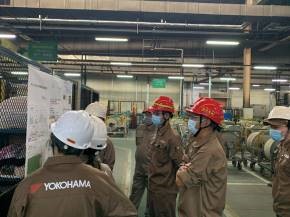
Safety patrols by the general manager
Managerial diversity
Managerial positions are filled not only through internal promotion from within the company, but also through outside recruitment. Currently, the company has 25 managers, of which one is a female department manager and four are section managers.
Employment of people with disabilities and promotion of employee diversity
There is a legal requirement that at least 1.5% of a company’s employees must be people with disabilities. Currently, CSZY has seven employees with disabilities. CSZY does not discriminate on the basis of gender in its recruitment and treatment of employees.
Of the total workforce of 830 employees (as of December 31, 2022), 122 were female employees.
The Environment
Environmental management
We have set out an environmental policy and comply with laws and regulations related to environmental protection, save resources, and implement preventive measures against pollution. In order to become a plant that is trusted by local communities, we operate an environmental management system, ISO 14001:2015, and are making improvements to our environmental facilities in consideration of the environmental impact on local residents.
Environmental data
Move the screen to the left or right to see the table information
Category | FY2018 | FY2019 | FY2020 | FY2021 | FY2022 | |
---|---|---|---|---|---|---|
Waste disposed (t) | 554 | 885 | 651 | 1,504 | 1,487 | |
Proportion sent to landfill (%) | 0.0 | 0.0 | 0.0 | 0.0 | 0.0 | |
Landfill waste (t) | 0.0 | 0.0 | 0.0 | 0.0 | 0.0 | |
Energy use (oil equivalent: kl) |
Electric power | 7,837 | 9,723 | 10,973 | 14,217 | 14,201 |
Fuel | 4,152 | 4,861 | 5,820 | 7,593 | 7,864 | |
Total | 11,457 | 12,698 | 15,543 | 21,810 | 22,065 | |
Greenhouse gas emissions (1,000t-CO2) | 29.1 | 32.0 | 39.3 | 38.6 | 51.1 | |
Water usage (1,000m3) | 117 | 133 | 175 | 232.1 | 232.5 |
- FY: January to December
- Greenhouse gas emissions were calculated based on the Calculation and Reporting Manual for Greenhouse Gas Emissions jointly published by the Ministry of the Environment and the Ministry of Economy, Trade and Industry, Japan. Calculation of emissions from overseas business locations in FY2015 was based on the Greenhouse Gas Protocol Initiative.
Reporting on chemical substance management status (Pollutant Release and Transfer Register (PRTR) Law compliance)
Chemical substances are managed in accordance with the chemical substance management regulations of the Plant prepared according to the laws.
We have prepared the oil and chemical management guideline CSZY-EPD-017R02.
Noise and emissions
We conduct measurements four a year in accordance with the regulations of the regional government. With respect to all measurements that have been taken thus far, the environmental regulation values on all items fall within the specified scope.
As a result of both the national “Action Plan for Winning the Blue-Sky War,” and the three-year emission controlplan put forward by the Suzhou National New & Hi-Tech Industrial Development Zone, the regulatory environment regarding emissions has stiffened. In undertaking our business activities, the company has worked together with the Suzhou City administration in order to meet such demands.
Environmental activities
In FY2022, we participated in the Lake Taihu fry release activity. Other activities included biodiversity activities (twice), sapling tray sharing activities and tree planting activities at the Forever Forest.
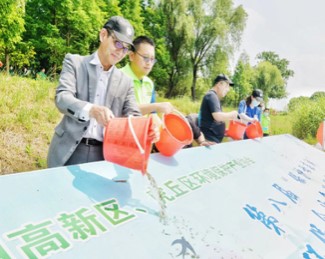
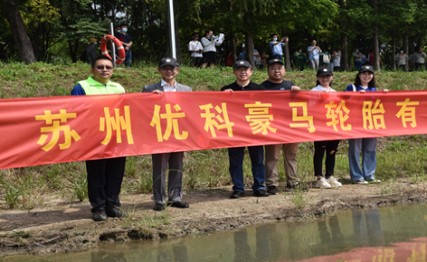
Jun 2, protection of Lake Taihu and fry release activity held by the Environmental Association.
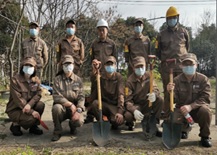
On March 10, 15 employees conducted a seedling-dispersing activity at Forever Forest.
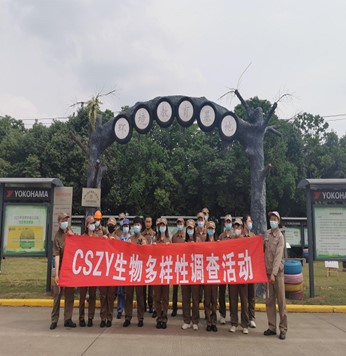
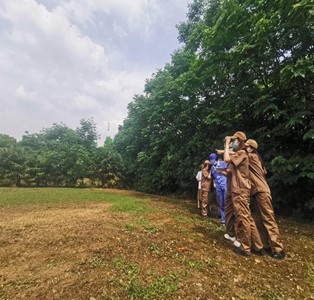
On May 27, 2022, the 14th biodiversity activity was held. Twenty-three new employees participated in this activity, conducting biodiversity surveys, measuring seedlings, and picking up seeds.
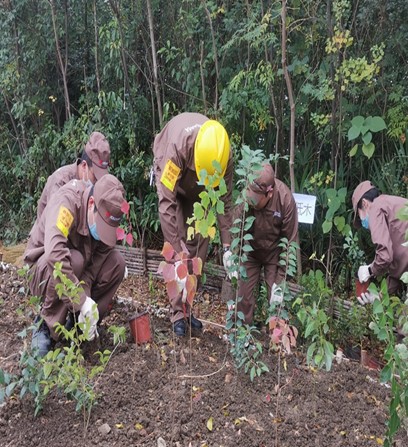
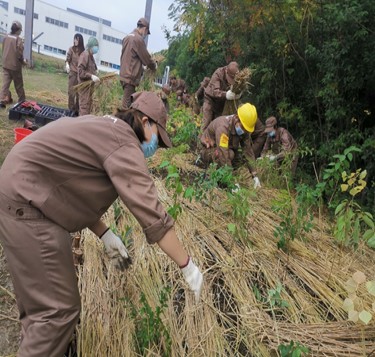
On November 18, 2022, the Forever Forest planting activity was held. Twenty new employees participated and planted 225 trees (45 m2 area).
Fair Operating Practices
Corruption prevention
CSZY is working to promote effective personnel rotations and other measures in order to make the flow of goods, information and money more transparent.
Each month, the Internal Control Office conducts an operational audit, and it establishes whether or not each of the subject operations is being carried out in accordance with instructions. Such work also seeks to verify the suitability of those operational processes that are subject to audit measures. Furthermore, the company is also working to build up a mutual surveillance structure through the organizing of whistle blowing systems and the installation of suggestions boxes, etc.
In 2022, the third step work of internal control was implemented to organize work flow, identify risks, and improve risks related to material purchase application, quotation comparison, order application, warehouse entry/export control, and disposal control.
Responsible participation in political affairs
Besides reporting to the relevant company committees all matters relating to revisions in the law, regulations or ordinances, once such has been scrutinized by the Internal Control Office, the company asks its attorneys for legal advice regarding all matters that relate to various contractual obligations or require specialist know-how.
Regularly collect laws related to company management and send them to relevant departments. Ensure compliance with laws during the implementation of each operation.
Fair competition
With respect to suppliers (both domestic and overseas) seeking to engage in business transactions with CSZY, the company provides fair, impartial opportunities for participation in an open manner.
On May 27, 2022, the Company issued a management guideline on how to comply with competition laws.
Promotion of social responsibility within the company’s scope of influence
We provide open, fair, and equitable entry opportunities for domestic and foreign suppliers who wish to do business with us.
Respect for intellectual property rights
We provide open, fair, and equitable entry opportunities for domestic and foreign suppliers who wish to do business with us.
Consumer Issues
Ensuring product quality and product safety
In line with our quality policy of “Providing consistently high- quality products so that customers all over the world can purchase our products with complete peace of mind,” we implement our quality management system effectively in accordance with the IATF 16949:2016 standard and customers’ requirements.
- External audits: 9 in total (all passed), maintaining customer satisfaction.
・OE audits: In addition to BMW, Mazda, and other traditional car manufacturers, the Company newly received and passed audits from New Energy Source (Beijing New Energy Source, NIO Motors, Guangqi Passenger Vehicle, etc.).
・REP customer audit: TUHU passed the audit requested by a third party, TUV.
・Accreditation: Passed IQA Brazil accreditation audit for the first time other than CCC accreditation. - Zero OE complaints.
Continuous promotion of PFMEA improvement activities (21 cases completed), achieved target of halving the number of process errors. - Completed improvement activities for recurrence prevention and proactive prevention as planned.
Y (yellow) to B (blue) (6 cases), POKAYOKE: (13 cases), including 2 cases of B2 conversion and 11 cases of prevention. - Identification of weak points by all inspectors and improvement of inspection accuracy through the use of eye trackers.
Improvement of inspection environment, inspection methods, inspection standards, and inspector evaluation methods.
Reduction of missed inspection rates through the above.
Improving after-sales services and customer satisfaction
Tire quality not only meets YRC standards, but also the quality standards of our local customers.
Through the improvement activities, the number of tire returns in the REP market is clearly decreasing and gradually improving from the customer satisfaction level in 2021.
Education and awareness-raising
To raise quality awareness among all employees, quality prediction training (QYT) was conducted once per day at each process, SOPs and other rules were correctly understood and followed, process improvements were made from the customer's viewpoint, and quality on-site follow-up was conducted by the general manager.
In April 2021, quality awareness training was provided to managers and team leaders, and in November, all employees received quality fraud prevention training.
In addition, the following activities were conducted as part of Quality Month activities.
(1) PFMEA risk analysis improvement activities
(2) QYT contest
(3) FM reduction activities(Day shift deploys cleanup activities at the site work area, cleaning up everything not related to the site and production)
(4) General manager quality patrol
(5) Quality Day Activity
(6) OPL contest
Community Involvement and Development
Participation in local environmental activities
On June 2, 2022, we participated in the activities held by the Environmental Association for the protection of the mother lake and the release of fry. At the same time, we also participated in environmental protection volunteer activities, " Environmental Protection Charity & Eco-Park " and other activities.
Plant tours
Applications for plant tours are accepted at any time by the Administration Department in accordance with the "Rules for Accepting Visitors”.