Head Office and Hiratsuka Factory (HQ-Hp)
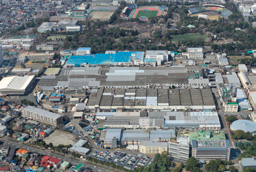
In March 2023, we relocated and integrated our head office functions from Minato-ku, Tokyo to the Hiratsuka Factory for the purpose of improving operational efficiency and reforming work styles by consolidating functions.
Business activities(Hp)Design, basic research, development and evaluation of aircraft parts, sporting equipment, adhesives and sealants, conveyor belts, marine hoses, fenders and other industrial products
Total site area255,656 m2 (including Adhesives and Sealants Plant)
Number of employees(HQ-Hp)2,454 (as of March 2023)
Location(HQ-Hp)2-1, Oiwake, Hiratsuka City, Kanagawa 254-8601, JAPAN
Contact for consultation and complaintsGeneral Affairs Group, Hiratsuka Facilities Dept. Tel: +81-463-35-9501 Fax: +81-463-35-9746
Message from the General Manager
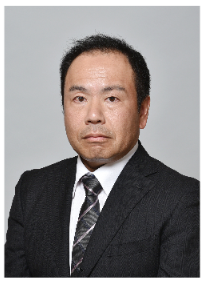
Tomoaki Miyamoto
While continuing to serve as a “base for the dissemination of technologies and monozukuri manufacturing expertise throughout the Yokohama Rubber Group,” the Hiratsuka Factory is also aiming to be a “factory that maintains the affection and unwavering trust of both customers and the community,” in line with Yokohama Rubber’s CSR Vision. Within this strategic framework, in the environmental sphere the Hiratsuka Factory is focusing in particular on reducing leakage and noise pollution, which can have a pronounced negative impact on the local environment, to zero, while in regard to safety the Hiratsuka Factory will be striving to eliminate accidents that are serious enough to require employees to take time off work, by ensuring that everyone who works at the Hiratsuka Factory puts safety first; in addition, as a factory belonging to a company that plays a key role within the automotive industry, the Hiratsuka Factory will also be seeking to reduce road accidents in which people are injured to zero. In terms of disaster prevention, we are working to improve the level of fire and disaster prevention based on our internal guidelines, and to build a BCP to prepare for disasters as a priority issue.
Furthermore, in every aspect of our business operations our actions will embody not only strict adherence to compliance-related regulations, we also act with the motto of "coming home with a smile every day" with an awareness of compassion for people, customer satisfaction, employee satisfaction and social contribution.
In FY2022, as in the previous year, activities will continue to be conducted within COVID-19, and unfortunately we have had to cancel various events that serve as opportunities for exchange. Despite these circumstances, we are continuing to carry out steady activities within the company, such as seedling cultivation at the Millennium Woods.
We have also completed the relocation of our head office in March 2023.
We will make preparations for the new office to be appreciated by employees and customers who commute to Hiratsuka, as well as by the local community.
We will also continue to engage in various CSR activities to contribute to the development of the Hiratsuka area.
Organizational Governance
Publicizing and sharing policies and issues
In that it represents a combined location, the Head Office and Hiratsuka Factory hosts multiple business departments, production plants and R&D facilities. Close attention is thus paid to thoroughly publicizing policies and issues that involve the entire company. We also strive to improve communication.
We strive for smooth plant management by making the director's policies and safety and environmental policies known at the morning meeting each term, and by making various performances known and sharing topics, etc. at the monthly plant meeting.
Improved functionality through management systems
We appropriately operate safety and environment in accordance with OSHMS and ISO 14001 management systems. We also implement continuous improvement through the PDCA cycle in the management system.
Human Rights
We provide opportunities for all employees to take compliance studies and learn about respect for human rights.
In addition, the Corporate Compliance Department has distributed to each employee a compliance card that describes the "Action Guidelines" to be followed by all employees of the Yokohama Rubber Group, in order to raise the level of awareness of respect for human rights.
Labor Practices
To ensure compliance with laws and regulations, we conduct monthly compliance training for each department, striving to increase employee knowledge and awareness.
In addition, in order to realize appropriate working hours, labor and management check working hours, etc., and the top management of labor and management conducts patrols to ensure proper management of work styles.
Furthermore, to improve the workplace environment, labor and management discuss items for improvement and promote improvements. In response to COVID-19, remote work is encouraged and a remote work environment has been created. Through these various measures, we are continuing to create an environment in which employees can work with peace of mind.
Promotion of gender equality
In fiscal 2022, the ratio of female staff in career-track positions stood at 21.2%.
We will continue to promote the hiring of female employees and promote work-life balance through the use of childcare leave and shorter working hours, the use of hourly paid leave system, flextime system and telecommuting system.
Promotion of employment of people with disabilities
As of the end of December 2022, the employment rate of persons with disabilities was 3.23%.
We will continue to promote the employment of people with disabilities and work to create a workplace environment where people with disabilities can work with vigor and enthusiasm.
Occupational safety and health management
Since the Hiratsuka Factory acquired Occupational Safety and Health Management System (OSHMS) certification in July 2010, we have conducted OSHMS-based occupational safety and health management. This work has been mainly built around continuous risk assessment and KY (Hazard Prediction) activities, etc.
When new operational processes are introduced or changes are made to existing operations, we hold “open work observations,” which allow many employees to witness work practices and identify hidden risks. We do this so as to further work improvement that makes work practices even safer.
Furthermore, we comply with safety and health statutory requirements, and proactively promote both employees’ acquisition of qualifications and educational activities. We also work to develop human resources and prevent disasters.
Traffic Safety
In order to reduce the number of traffic accidents, we provide traffic safety guidance and conduct road safety seminars for all employees twice a year. Each month, we conduct traffic safety education and other activities at each workplace.
Furthermore, three times a year before long vacations, we raise awareness of traffic safety by showing an educational video about traffic safety in the cafeteria during lunch time. We are aware of our responsibility as a company that plays a part in the automotive industry, and are working to prevent traffic accidents.
Health management
We follow up to ensure that 100% of our employees receive the various medical examinations required by law, including regular medical checkups and special medical checkups.
We also provide mental health care to employees who have concerns about their work or private lives by offering counseling opportunities by Industrial counselors.
COVID-19 infection control measures were continued to prevent the spread of infection within the company.
The Environment
Environmental management
The Hiratsuka Factory continues to operate environmental management based on ISO 14001 environmental management system certification, which was acquired in July 1999.
From fiscal 2012, it converted to an environmental management system integrating the entire company as one site of Yokohama Rubber. We will continue to deploy activities based on the company-wide environmental policy.
As the Hiratsuka Factory holds a wide range of business organizations, from plants with different production methods to the technical research and development department of the entire company, it divides them into 10 environmental blocks to advance daily environmental improvement activities under the Hiratsuka Factory Environmental Policy in compliance with the company-wide environmental policy.
Environmental data
Reduction of greenhouse gas emissions
Greenhouse gas emissions
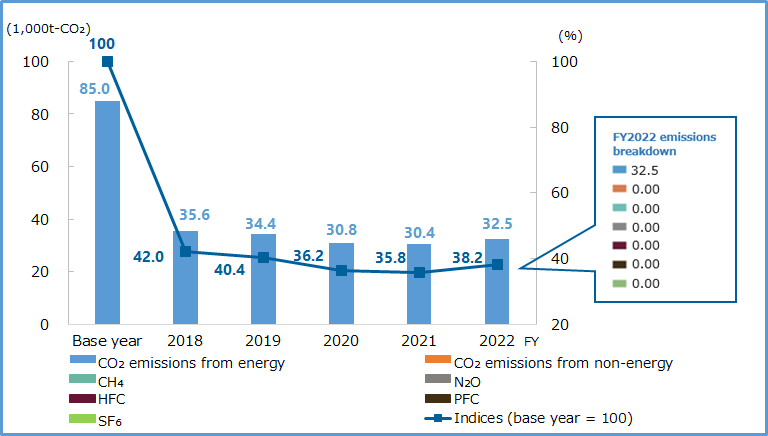
- The base year is defined as 1990 except for HFC, PFC and SF6, where the base year is 1995 as per the Kyoto Protocol.
- Method of calculation of greenhouse gases (GHG): this is in compliance with the “Calculation and Reporting Manual for Greenhouse Gas Emissions” issued by the Ministry of the Environment and the Ministry of Economy, Trade and Industry.
Note that GHG emissions associated with purchased power in FY2009 were calculated using the Table of Emission Coefficients by Power Company (Ministry of the Environment).
Effective use of resources / Reduction of waste
Waste output
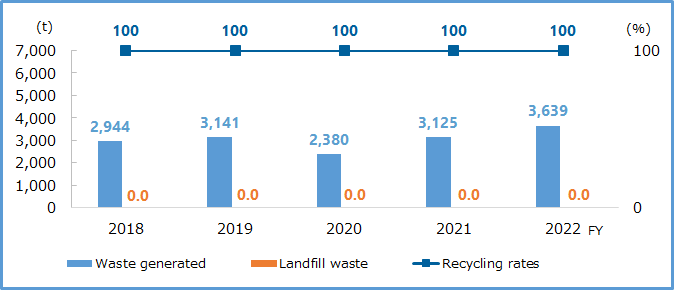
Water Usage
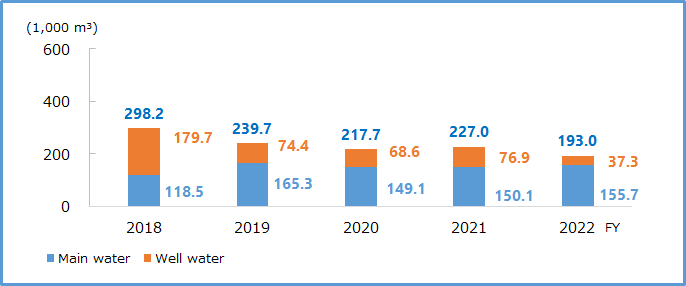
Measures for discharges into water, air and soil
Data related to water contamination
Move the screen to the left or right to see the table information
Drain | Item | Regulatory values | Voluntary standard values | FY2022 results | ||
---|---|---|---|---|---|---|
Average | Maximum | Minimum | ||||
Hiratsuka Factory | pH | 5.0~9.0 | 5.18~8.7 | 7.8 | 8.3 | 7.3 |
BOD concentration (mg/l) | 600 | 430 | 55.25 | 100 | 18 | |
SS concentration (mg/l) | 600 | 190.0 | 48 | 86 | 16 | |
Animal and plant oil concentration (mg/l) | 30 | 15.0 | 6.4 | 27 | 1 | |
Mineral oil concentration (mg/l) | 5 | 3.1 | 1 | 1 | 1 |
- In accordance with the Hiratsuka Municipal Sewerage Ordinance.
Air pollutants (NOx, SOx)
Move the screen to the left or right to see the table information
Substance | NOx emissions (t/year) | SOx emissions (t/year) |
---|---|---|
Hiratsuka Factory | 2 | ― |
Facility | Substance | Regulatory values | Voluntary standard values | FY2022 results | ||
---|---|---|---|---|---|---|
Average | Maximum | Minimum | ||||
Hiratsuka Factory Boilers 1 |
Nox (ppm) Soot and dust (g/h) |
150 635.4 |
31.0 51.9 |
22 4.4 |
22 4.4 |
22 4.3 |
Hiratsuka Factory Boilers 2 |
Nox (ppm) Soot and dust (g/h) |
150 635.4 |
31.0 51.9 |
22.5 4.5 |
23 4.5 |
28 4.4 |
Hiratsuka Factory Boilers 3 |
Nox (ppm) Soot and dust (g/h) |
150 635.4 |
31.0 51.9 |
22 4.8 |
23 4.9 |
21 4.7 |
Hiratsuka Factory Boilers 4 |
Nox (ppm) Soot and dust (g/h) |
150 635.4 |
31.0 51.9 |
23 4.9 |
24 5.1 |
22 4.6 |
Hiratsuka Factory Boilers 5 |
Nox (ppm) Soot and dust (g/h) |
150 635.4 |
31.0 51.9 |
23 4.4 |
23 4.6 |
23 4.2 |
Hiratsuka Factory Boilers 6 |
Nox (ppm) Soot and dust (g/h) |
150 635.4 |
31.0 51.9 |
23 4.7 |
23 4.9 |
23 4.5 |
- In accordance with the Air Pollution Prevention Law and Kanagawa Prefectural Ordinance.
Reporting on chemical substance management status (Pollutant Release and Transfer Register (PRTR) Law compliance)
The Hiratsuka Factory verifies whether secondary materials and auxiliary materials contain chemical substances subject to Safety Data Sheet (SDS)requirements, and in the case of substances where the amounts handled exceed the thresholds specified by the PRTR Law, annual reports are submitted to the national (or prefectural) authorities and safety impact assessment is performed.
Regarding the handling of substances pursuant to the PRTR Law, please refer to the Safety Evaluation Table of Domestic Production Bases.
Pollution prevention
We have established self-administered values that are even stricter than regulated targets so as to strictly observe all environmental laws and ordinances concerning air pollution, water contamination and noise, etc. We take steps to monitor and measure these values.
Furthermore, to ensure that no sensory discomfort resulting from noise, vibrations and odors, etc. is caused to neighborhood residents, we have established monitoring points outside the factory grounds and are working to prevent such issues.
With respect to PCB waste within the factory, it is suitably handled in accordance with the relevant laws and regulations.
Use of sustainable resources
We are taking steps to reduce overall volumes year-on-year by placing a top priority on the goals and targets of the ISO 14001 management system with respect to reductions in industrial waste, organic solvents, greenhouse gas emissions and water usage.
Alleviating and adapting to climate change
During "Energy Saving Month" in February and "Environment Month" in June, we set up priority measures in each of our original operations and report on energy saving achievements, while division managers of each block conduct environmental patrols.
Environmental protection, recovery of natural habitats
Since fiscal 2013, we have been conducting biodiversity conservation activities to protect water resources in the local Kaname River system.
Employees have participated in a series of hands-on monitoring activities to examine the environment of the Kaname River, with a cumulative total of 346 employees taking part.
Currently, activities are being conducted in a satoyama in the city located upstream of the Kaname River.
Specifically, with the objectives of recharging the water source of the Kaname River and restoring the original landscape of the satoyama, we are conducting conservation activities in collaboration with local groups and university laboratories, including the installation of handmade biotopes, and monitoring changes in the ecosystem.
Furthermore, since FY 2017, we have installed a dragonfly pond on the Hiratsuka Factory premises as a familiar activity site to observe the connections among dragonflies and other living creatures.In March 2017, the Hiratsuka Factory received the " Association for Business Innovation in Harmony with Nature and Community Certificate® (ABINC certification)" as a biodiversity-conscious plant in recognition of these biodiversity activities and the ongoing CO₂ absorption and fixation amount survey conducted in conjunction with the growth of the Yokohama Forever forest planted around the plant in 2007.

False bindweed growing wild on the grounds
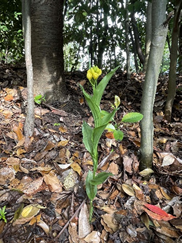
Golden Orchid (effect of the Forever Forest activities)
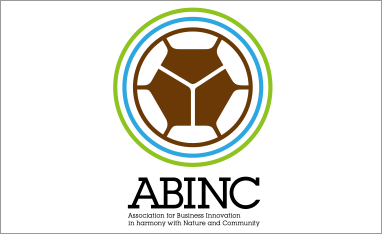
ABINC logo mark
Fair Operating Practices
Impartial and fair selection of business partners
To ensure fair selection of suppliers, we conduct a survey on whether or not there are any personal relationships between the targeted suppliers and our employees when we hire new suppliers.
Other selection is based on economic rationality, taking into consideration the supplier's quality, price, supply stability, technological development capabilities, and CSR and environmental considerations.
Establishment of a “Procurement Code of Conduct” and its thorough implementation
With the “Basic Procurement Policy”, we prepared the “Procurement Ethics (Rules for Procurement Staff)” to indicate matters to be noted by procurement staff when conducting fair and impartial transactions and unethical practices that must not be engaged in. These ethics were combined with the “Basic Procurement Policy” to become the “Procurement Code of Conduct”.
We are working to ensure comprehensive awareness of compliance issues through workplace-based classes, which are held on a regular basis.
Deployment of CSR activities for business partners
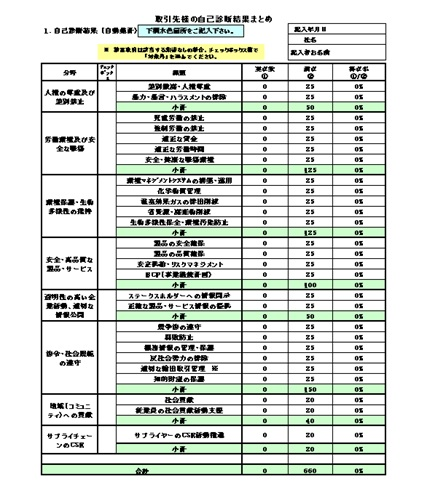
In 2022, we held an online (webinar-style) CSR supplier briefing session for the first time.
The briefing covered such topics as "CSR Report, CSR Guidelines," "Mid-Term Environmental Plan," "Corporate Social Responsibility and Human Rights," and "Workplace Safety," and was attended by 398 suppliers.
Consumer Issues
At our Head Office and Hiratsuka Factory, we are deeply involved in all corporate activities such as planning, manufacturing, evaluation, and sales of the products and services we deliver to our customers.
We aim to realize a sustainable society together with our consumers in addition to tackling those tasks from the viewpoint of CS (Customer Satisfaction).
Therefore, we value the valuable opinions we receive from our customers and strive to expand our communication by disseminating information about our corporate initiatives through various means.
Contact Information for Inquiries
The contact information for inquiries is disclosed at the following address on our official website.
https://www.y-yokohama.com/global/contact/
Community Involvement and Development
Regional activities
We have continuously participated in volunteer activities organized by local groups, such as tree planting and riverbank cleanup, but unfortunately we refrained from such activities in fiscal 2022 due to COVID-19.
Disaster-prevention activities
Unfortunately, due to the effects of COVID-19, the annual fire-fighting competition organized by the Hiratsuka City Hazards and Safety Committee was cancelled in fiscal 2022. We also refrained from activities in cooperation with the local community, such as supporting disaster drills at the Hiratsuka School for the Visually Impaired, which is located adjacent to the Hiratsuka Factory and with which we have a disaster countermeasure cooperation agreement.
On the other hand, the annual disaster drills at the Hiratsuka Factory were conducted in the form of desktop drills to prevent the spread of COVID-19.
Regional contributions
- We continue to support Shonan Bellmare, a local J-League team, under our CSR partnership agreement.
- Once a month, employees carry out cleaning activities around the perimeter of the factory.
Regional exchanges
Unfortunately, we refrained from activities in FY2022 due to the COVID-19 disaster.
Results of a questionnaire survey about our local communication events
In consideration of preventing the spread of COVID-19, we have cancelled the regional communication meeting.
List of FY2022 Regional Contributions / Community Activities
Hiratsuka Factory History Tour
We have decided to cancel the Hiratsuka Factory history tour in consideration of preventing the spread of COVID-19.
Volunteer activities
In consideration of preventing the spread of COVID-19, various volunteer activities have been cancelled or refrained from.
Provision of Yokohama Forever Forest seedlings
April 24, 2023: 1,000 seedlings for social welfare corporations
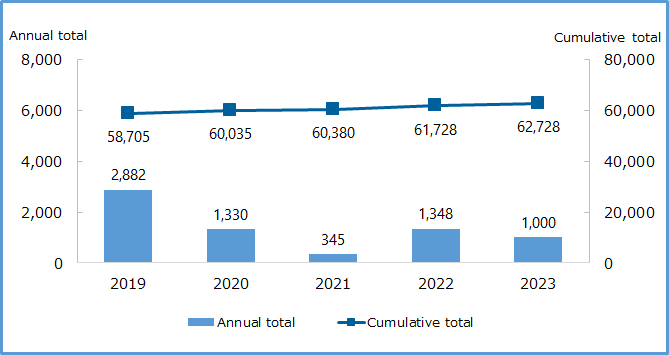
Support for education
We support Hiratsuka School for the Deaf and Hiratsuka School for the Blind as a member of their school management council.
Local event support, donations, and participation
We refrained from activities due to COVID-19.