Labor Practices
Occupational Health and Safety
KPI
Responsible Departments
Our position and Targets
Review of FY 2022 Activities
Introduction of Initiatives
Future challenges
KPI
Move the screen to the left or right to see the table information
Item | FY 2021 results | FY 2022 results |
---|---|---|
Lost-time injury frequency rate (global, directly employed) |
(Consolidated) 0.18 Domestic 0.45 Overseas 0.07 |
(Consolidated) 0.24 Domestic 0.55 Overseas 0.10 |
Scope of application of Occupational Health and Safety Program | 100% | 100% |
Number of workers with a high risk of accident or illness | Zero | Zero |
Formal agreement with labor unions regarding occupational health and safety matters | Yes (at those business locations where there is a labor union) |
Yes (at those business locations where there is a labor union) |
Responsible Departments
Each business location
- Activities are conducted by each business location, and the Central Committee of Safety and Health that the Safety and Health Management Department serves as a secretariat implements company-wide policy discussions and activities.
Our position and Targets
Why is “Occupational Health and Safety” a critical issue to be addressed?
Explanation of the reason and background
We believe that the labor environment that allows workers to be able to work in a secure and safe manner constitutes a foundation for operations. As regards work-related accidents at the Yokohama Rubber Group in Japan and overseas, the accident frequency rate of the Group is lower when compared with that of the overall industry or the manufacturing industry, but not zero, and analysis of the causes of such accidents has revealed that many of them could have been prevented by taking precautions. As it is necessary to handle large machinery at our production plants due to the nature of our business, defects in equipment specifications or incorrect operation can lead to serious accidents; it is necessary to take appropriate safety measures. Additionally, with mental health issues accounting for an increasing proportion of long-term absences from work, we must properly look after the mental health of employees as well as their physical health. For this reason, at the Yokohama Rubber Group, we have defined occupational safety and health as a critical issue to be addressed.
Health and safety management system
In Japan, under the Central Safety and Health Committee chaired by the head of the CSR Division, each business site has its "Business Site Safety and Health Committee (legally mandated)" and each department and workplace have their "Department Safety and Health Committee. As safety and health activities are important initiatives for both the company and the union, we are promoting them in concerted effort between labor and management while sharing safety information with other companies and labor unions through interaction with the Japan Rubber Manufacturers Association or the Japan Rubber workers' union Confederation. We also share our activities with our subcontractors by having them join their respective committees. In addition, to create a workplace where employees can work in good health for a long time, we promote health and physical fitness based on “Collaborative Health” in cooperation with health insurance associations. Each overseas company has developed its own system in accordance with the laws of each country. The Safety and Health Management Department coordinates health and safety activities in Japan and overseas.
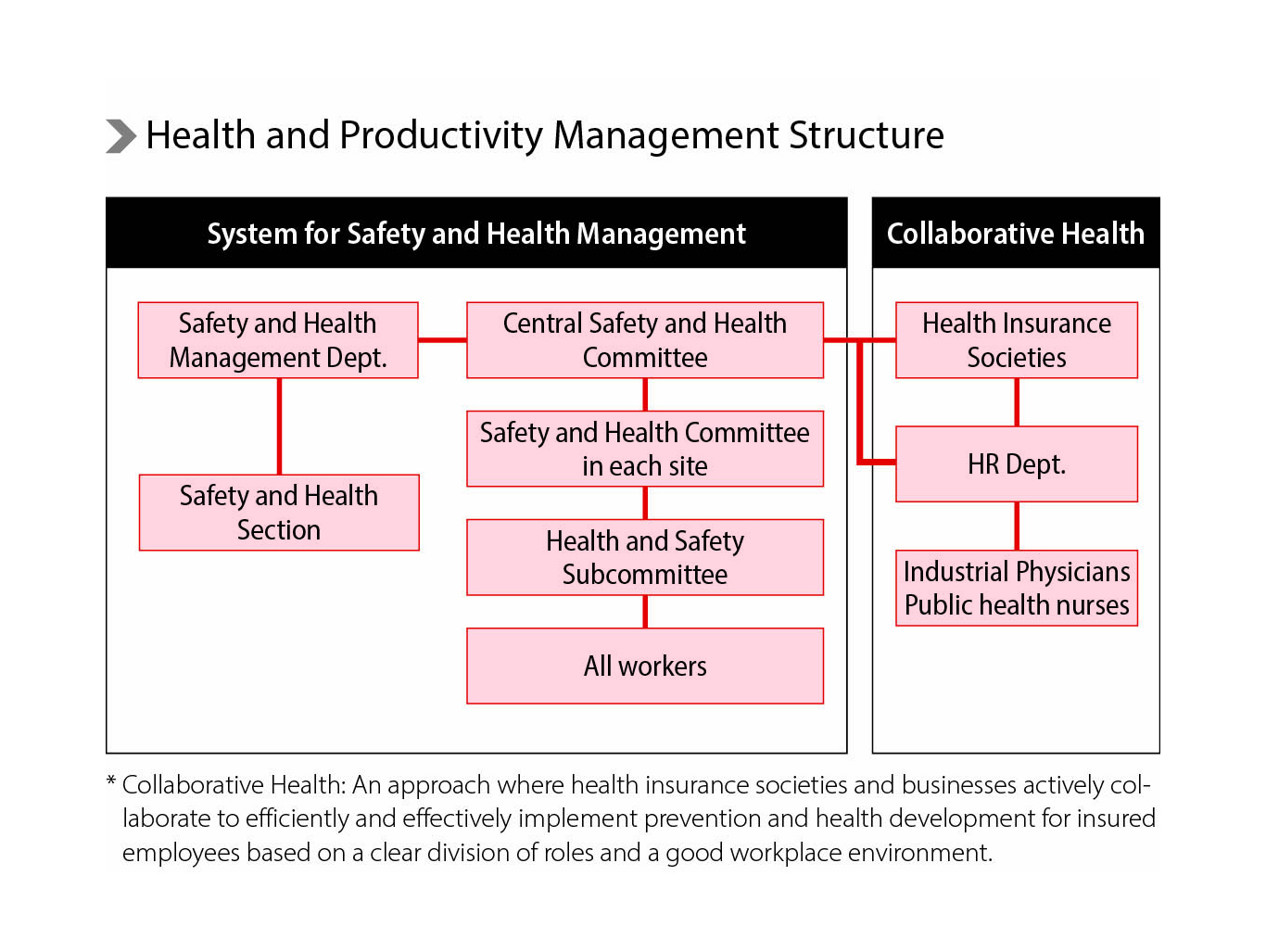
Vision and targets
- We will promote the creation of a safe and pleasant working environment and good health.
- We will foster a culture of safety to remove all hazards, aiming to achieve zero occupational accidents.
Measures to pursue our vision
We will implement the following seven initiatives to create workplaces that enable employees to work in a safe and healthy manner.
- Enhancement of equipment measures
Conducting risk assessments and creating facilities that do not allow either human bodies to be placed at hazardous sources, or their hands to reach them, in order to prevent the recurrence of similar accidents - Development of safety-conscious human resources
Aiming to develop people with the sensitivity to perceive hazardous events as dangerous through providing education on a one-on-one basis, increasing safety awareness, retraining workers to practice "stop/call/wait" and take countermeasures in response to risk causes, implementing hazard prediction training (KYT), and conducting near-miss (hiyari-hatto) detection and improvement activities, as well as providing experiential training - Development of standard work manuals
Conducting open work observation to identify all unsafe areas of insecurity and behaviors and review our standard work manuals - Promotion of physical and mental health
Strengthening measures for mental health (management of working hours, face-to-face guidance and work improvement suggestions for employees working long hours, education for improving communication skills through attentive listening training classes, and implementation of stress checks) - Improvements in workplaces
Chemical risk assessment, maintenance of personal protective equipment and facilities, improvement of work methods, rigorous implementation of 5S (seiri [tidiness], seiton [being organized], seisou [cleanliness], seiketsu [hygiene], shitsuke [discipline]) activities, and improvement of high temperature work environment - Prevention of traffic accidents
Conducting accident prevention activities and identifying high-risk points on commuting routes in order to achieve the target of zero accidents causing injury or death - Establishment of a safety and health platform
Enhancing checking functions by continuously using and steadily improving the occupational health and safety management system, and developing training system for each level, as well as conducting top safety diagnoses, safety patrols, and safety diagnosis, and monitoring the benefits of such measures
Review of FY 2022 Activities
The following activities were conducted to promote each initiative in FY2022.
1. Enhancement of equipment measures
We systematically and continually conduct risk assessments for all facilities and operations, and implement safety measures with a focus on the safety of the equipment. In parallel with these efforts, we operate a system for monthly follow-up on the number of risks and improvements. Top safety diagnoses are conducted by directors at our domestic plants. In addition, we are enhancing company-wide efforts to share information on disaster countermeasures to prevent recurrence of similar disasters.
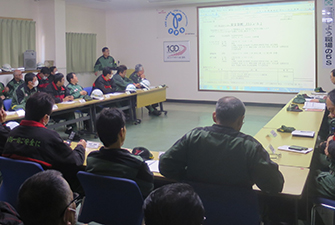
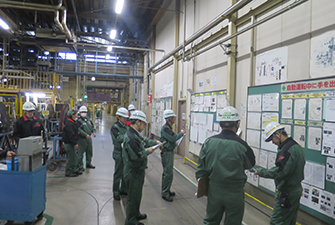
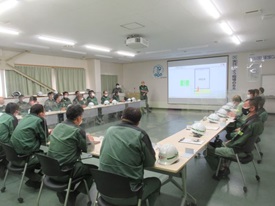
Safety diagnosis
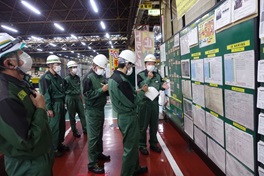
Top safety diagnosis
2. Development of safety-conscious human resources
We aim to develop people with the sensitivity to perceive hazardous events as dangerous. To this end, we provide hazard prediction training (KYT), which all employees practice every day, along with near-miss (hiyari-hatto) detection and improvement activities as well as experiential training called "Taikan Dojo," both of which are voluntary activities that all workers are encouraged to participate in. In addition, we continue to conduct safety education that emphasizes communication, in which supervisors talk with workers one-on-one to help them to understand the meaning of each task and are able to act more safely at their own discretion
In addition, as fellow workers, we have encouraged our employees, who are also our partners, to participate in these activities to prevent the occurrence of accidents and improve their safety levels.
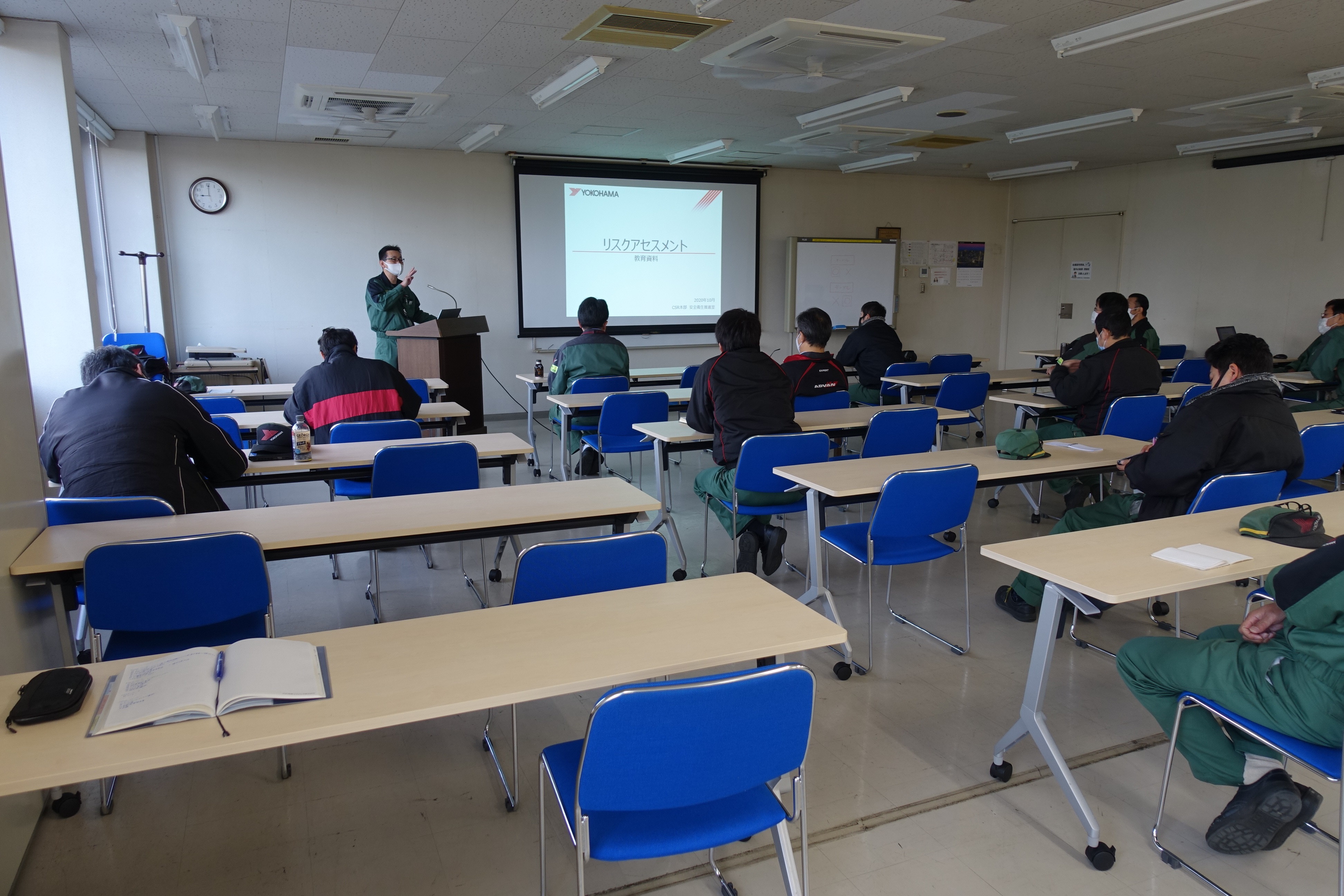
Risk assessment training
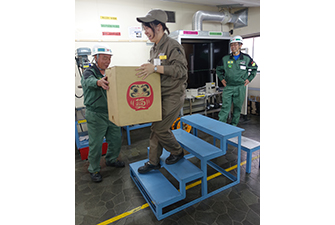
Hands-on safety drills with overseas plant safety personnel
(Hands-on experience of stairs with holding a load)
(Hands-on experience of stairs with holding a load)
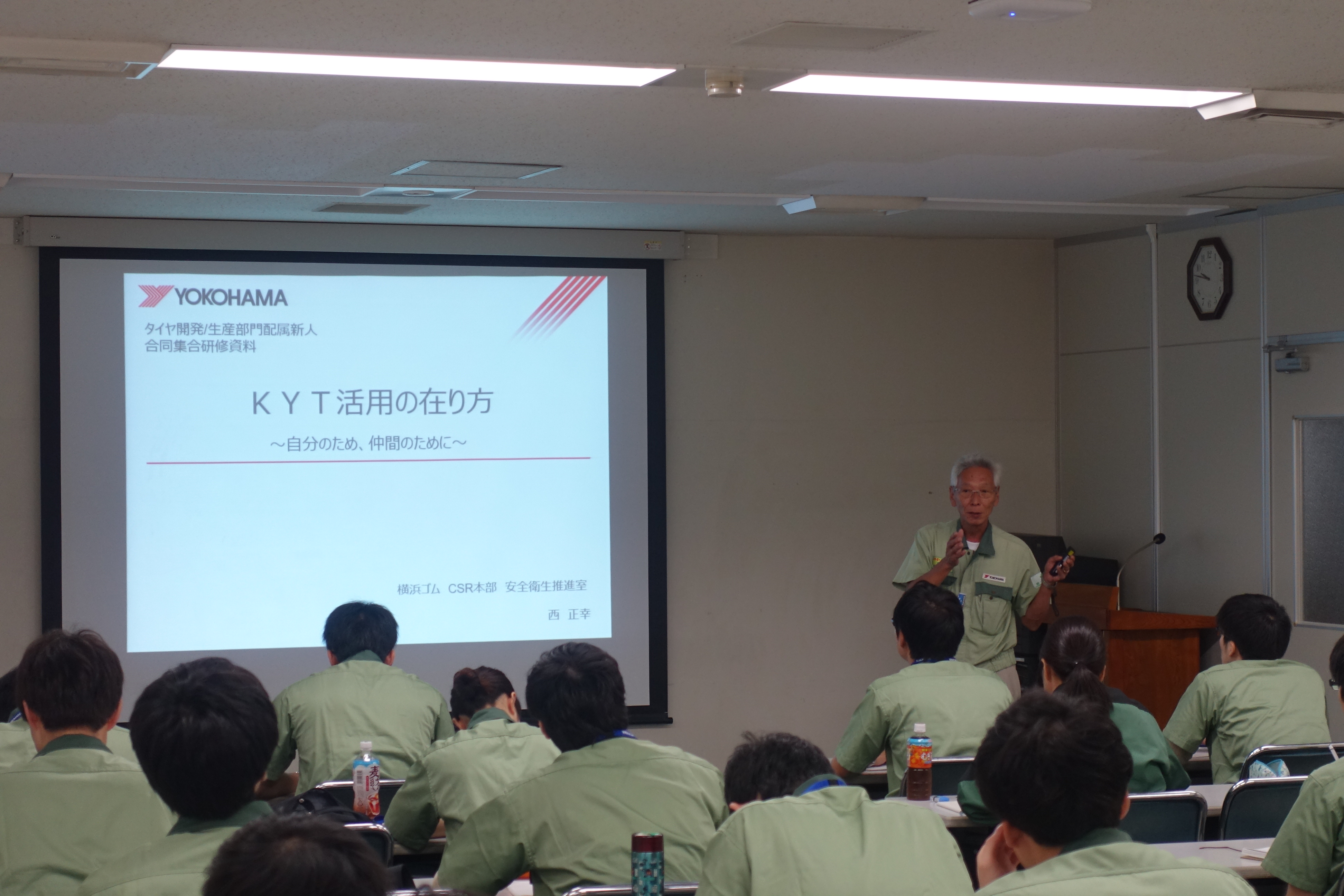
Newcomer KYT Training
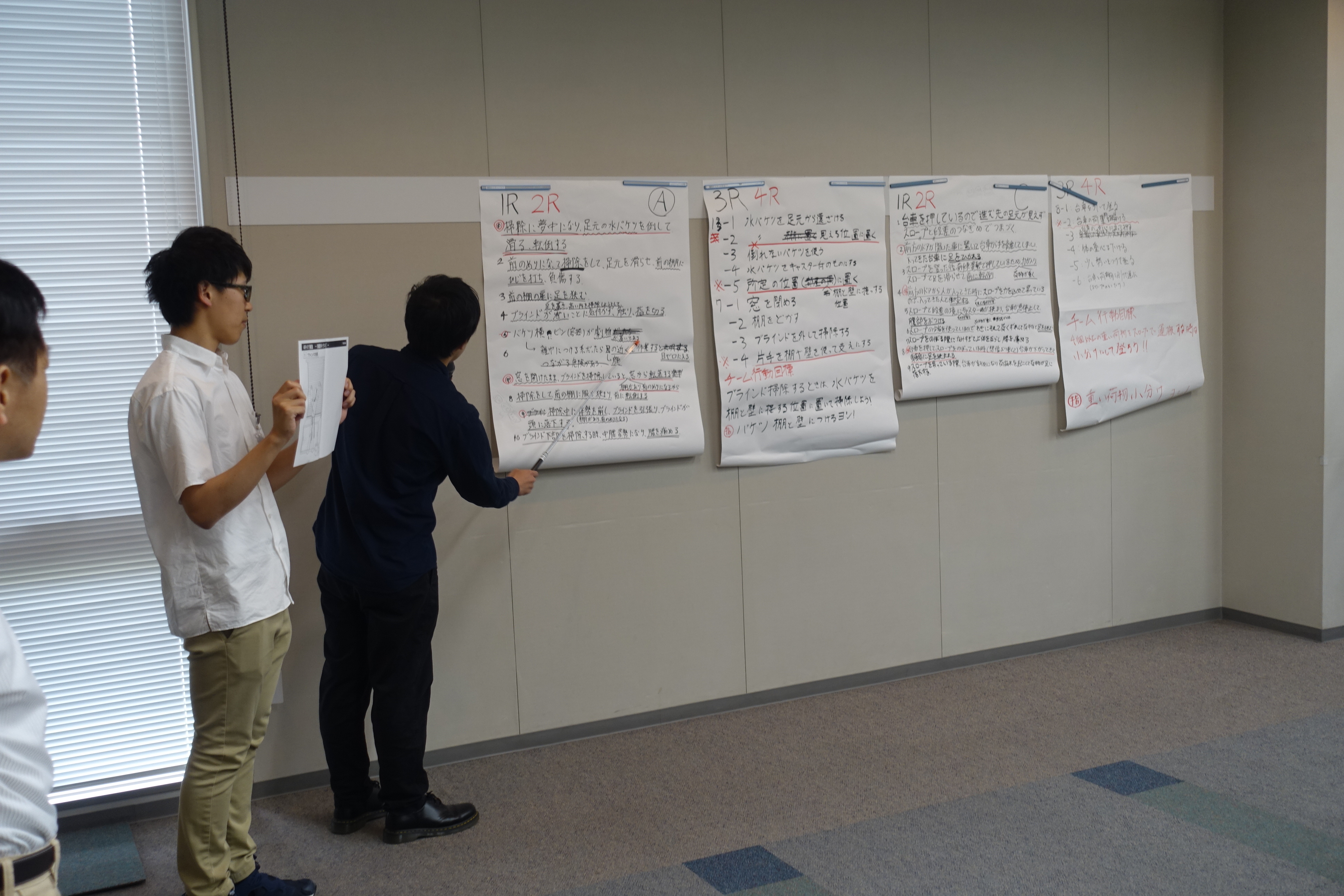
Techno-College
3. Development of standard work manuals
We systematically and continually conduct open work observation to identify all unsafe behaviors and areas of insecurity, and are working on the development of standard work manuals. At workplaces with workers from overseas, the standard work manuals are also provided in their native languages.
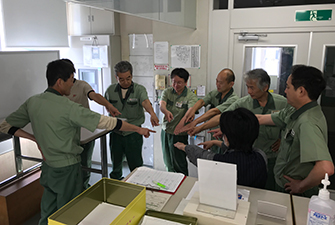
Singing the Safety Chant together before beginning work.
4. Promotion of physical and mental health
Our efforts in mental health initiatives include management of working hours through an attendance management system, face-to-face guidance and work improvement suggestions for employees working long hours, and education for improving communication skills through attentive listening training classes, etc. In addition, we began to conduct a stress check in FY2016. This has been practiced with the main purpose of preventing mental health issues among employees (primary prevention) by improving our workplaces to create pleasant working environment through assessing the level of workers' stress and making them more conscious of their own stress.
For the reinstatement of long-term absentees who have been absent due to mental health reasons, we conduct an interviews with them, and consult with their attending physicians, industrial physicians, public health nurses, and workplace representatives to discuss matters such as the means of reinstatement, timing, and work limitations in order to achieve a well-planned reinstatement. We have supported the reinstatement of employees at the Head Office and the Hiratsuka Factory in cooperation with the Jikei University Hospital and three industrial doctors for mental health; there are still not many companies staffed by industrial doctors for mental health.
Even after the reinstatement of an employee, regular three-party interviews are conducted between the employee, the industrial doctor, and the workplace representative, and continuous support will be provided with work-related restrictions gradually being lifted, until such restrictions are completely removed.
We also conduct activities to help employees quit smoking, and hold seminars on physical fitness in order to promote their health.
In FY2022, we signed a Memorandum of Understanding (MOU) with health insurance associations to establish a health and safety management system. We have introduced health applications, and held various events featuring health measurement, health-related quizzes, walking event, etc.
For the reinstatement of long-term absentees who have been absent due to mental health reasons, we conduct an interviews with them, and consult with their attending physicians, industrial physicians, public health nurses, and workplace representatives to discuss matters such as the means of reinstatement, timing, and work limitations in order to achieve a well-planned reinstatement. We have supported the reinstatement of employees at the Head Office and the Hiratsuka Factory in cooperation with the Jikei University Hospital and three industrial doctors for mental health; there are still not many companies staffed by industrial doctors for mental health.
Even after the reinstatement of an employee, regular three-party interviews are conducted between the employee, the industrial doctor, and the workplace representative, and continuous support will be provided with work-related restrictions gradually being lifted, until such restrictions are completely removed.
We also conduct activities to help employees quit smoking, and hold seminars on physical fitness in order to promote their health.
In FY2022, we signed a Memorandum of Understanding (MOU) with health insurance associations to establish a health and safety management system. We have introduced health applications, and held various events featuring health measurement, health-related quizzes, walking event, etc.

Stress check study session at Onomichi Plant
Health Promotion Activities at Mie Plant
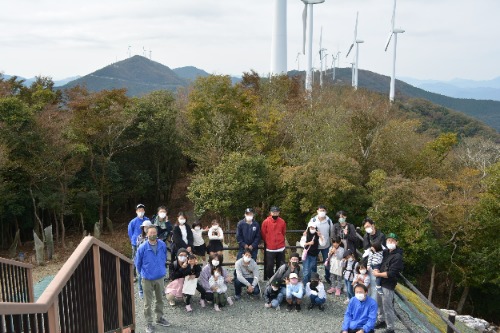
Labor-management co-sponsored hikes
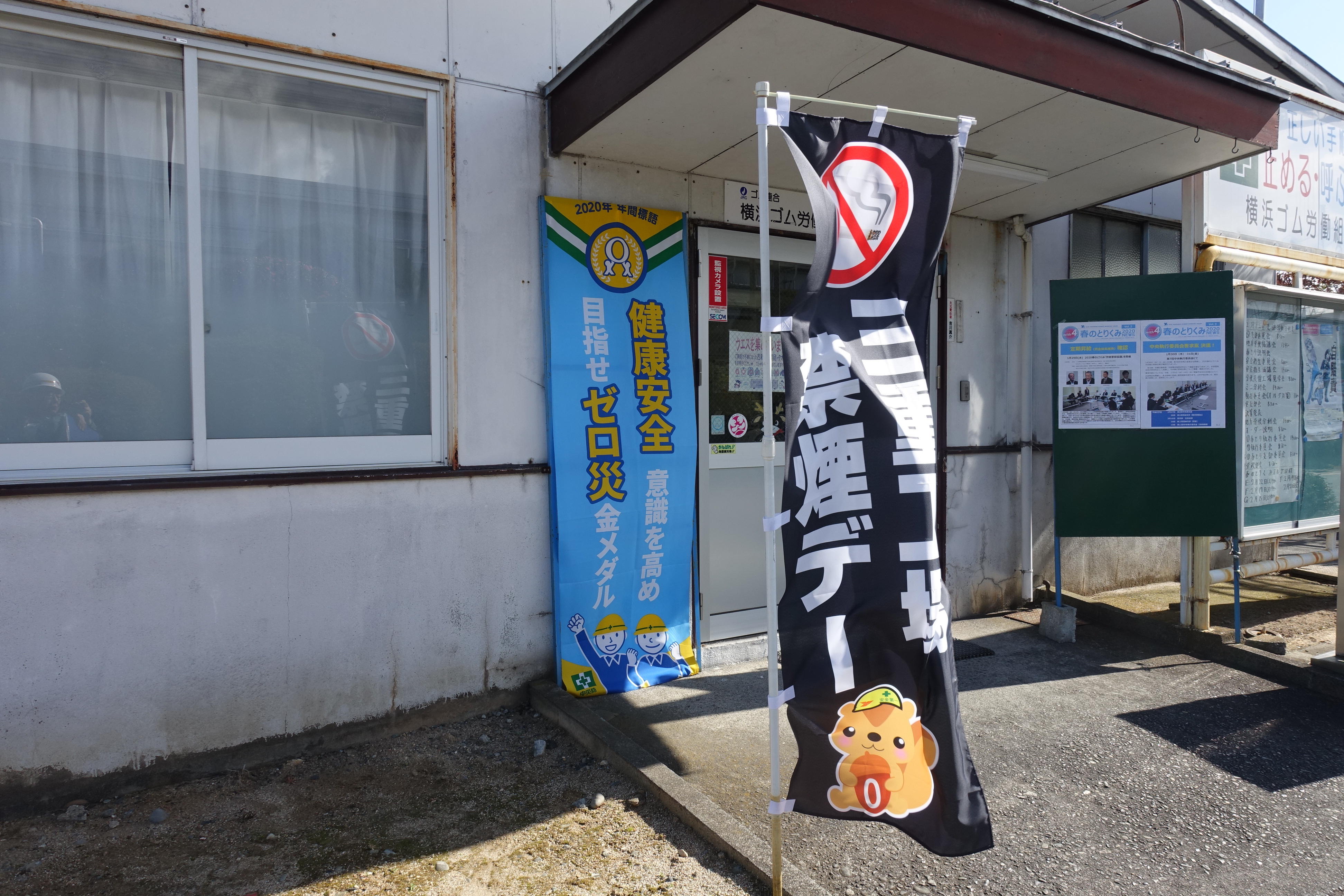
No Smoking Day at the Mie Plant
5. Environmental improvements in workplaces
At workplaces handling chemical substances, we conduct chemical risk assessment to prevent health disorders caused by chemical substances. We have also promoted the maintenance of equipment and provision of personal protective equipment, the improvement of working methods, and the maintenance of facilities to manage the maintenance of a comfortable working environment based on environment measurement results. In addition, based on the 5Ss (seiri [tidiness], seiton [being organized], seisou [cleanliness], seiketsu [hygiene], and shitsuke [discipline]) activities, we are promoting the manufacturing that creates only products that are needed and have no unsafe parts as many as needed.
Moreover, considering "life-threatening heat" we have been suffering in recent year, we view heat stroke as a disaster that can lead to fatal accidents just as injuries, and are measuring WBGT values at our workplaces, working to lower these values, such as by discharging hot air.
Moreover, considering "life-threatening heat" we have been suffering in recent year, we view heat stroke as a disaster that can lead to fatal accidents just as injuries, and are measuring WBGT values at our workplaces, working to lower these values, such as by discharging hot air.
- WBGT (wet-bulb globe temperature) value (heat index): It is an index focusing on heat exchange between human body and external environment (heat balance), which takes into account the three factors having significant impact on human body's heat balance: (1) humidity, (2) surrounding thermal environment including solar insolation and radiation, etc., and (3) temperature.
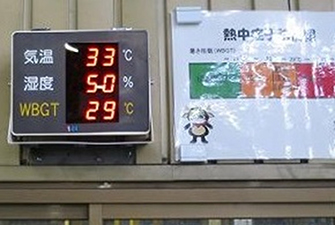
Visualizing the Workplace Environment with WBGT Meter*.
- WBGT meter: a device that measures and displays WBGT values
6. Preventing traffic accidents
At each of our business site, we hold traffic safety seminars by local police departments and conduct activities to raise awareness in cooperation with traffic safety-related organizations. In addition, we are working to raise traffic safety awareness through education using drive recorders and by
talking to people passing at the front gate to invite their attention to safety.
7. Establishment of a safety and health platform
We have acquired a certification for Occupational Safety and Health Management System (JISHA/OSHMS/ISO45001) at 18 (21) domestic and overseas business sites, with eight sites renewing their certification in FY2022. (The certification process is still ongoing at other business sites.)
We will continue to improve our management system and implement the PDCA (plan, do, check and action) cycle as we work to enhance our safety and health infrastructure.
As other initiatives, we work to ensure the safety of the equipment and devices regularly by conducing safety diagnosis by the Safety and Health Management Department at domestic factories twice a year.
We will continue to improve our management system and implement the PDCA (plan, do, check and action) cycle as we work to enhance our safety and health infrastructure.
As other initiatives, we work to ensure the safety of the equipment and devices regularly by conducing safety diagnosis by the Safety and Health Management Department at domestic factories twice a year.
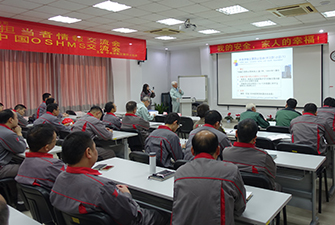
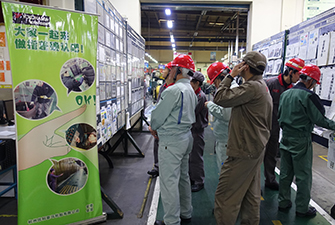
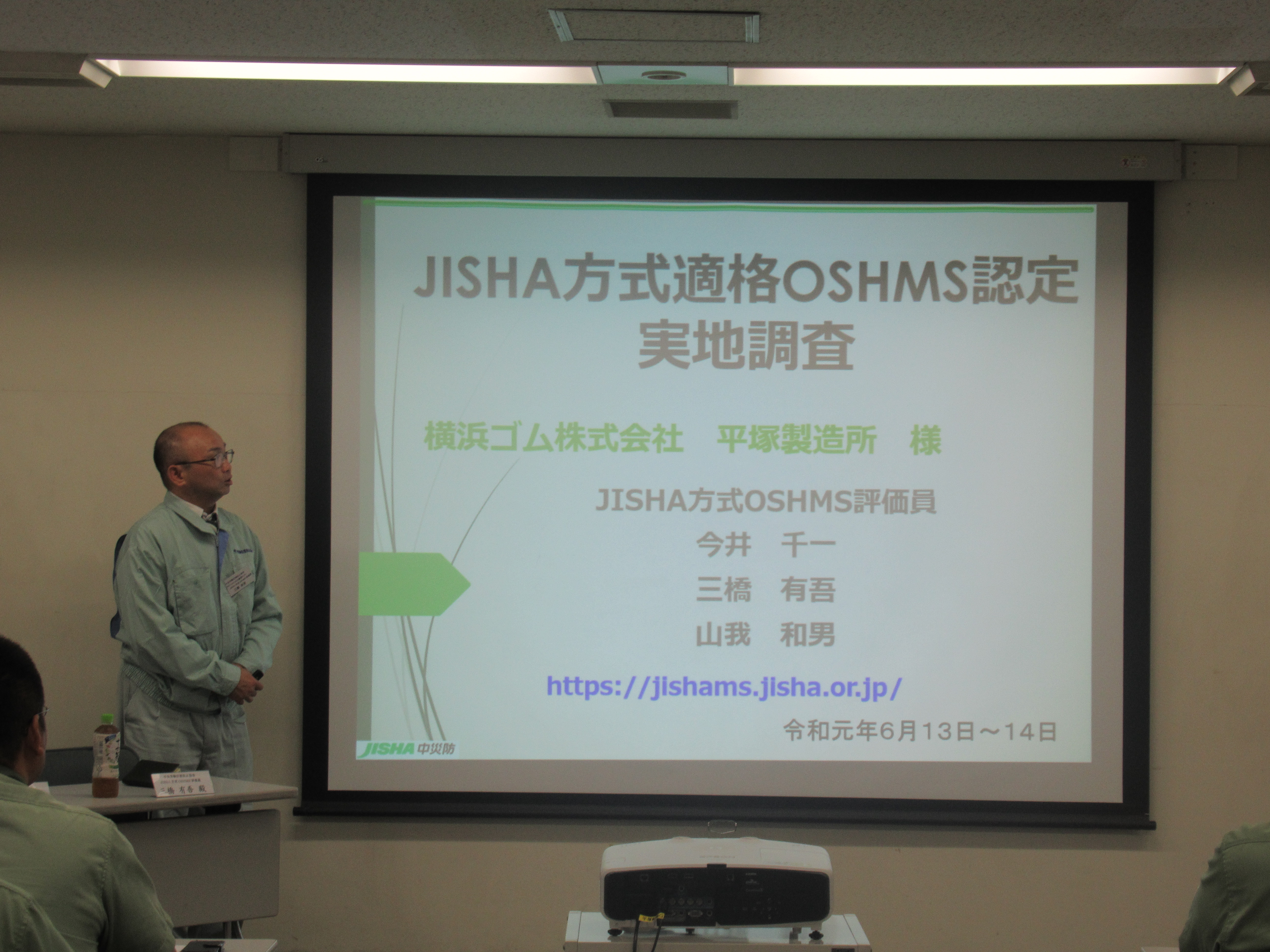

The frequency of occupational accidents was 0.24. We will continue our efforts to achieve zero accidents and zero risks.
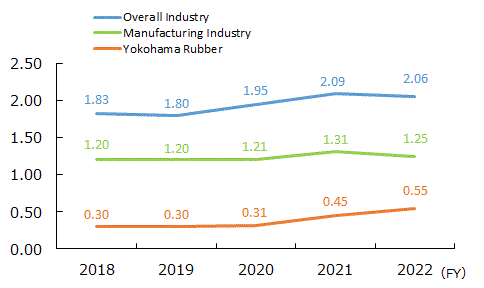
Frequency of Occupational Accidents (Lost-time injury frequency rate)
Descriptions of the figures
- Lost-time injury frequency rate = (number of work-related injuries / total working hours) × 1,000,000 hours
- All figures in the data represent annual aggregated values (from January to December)
- Figures for the overall industry (excluding general contracting business) and the manufacturing industry are based on the "Survey on Industrial Accidents" statistical table released by the Ministry of Health, Labor and Welfare
Introduction of Initiatives
In April 2019, we held a safety exchange meeting with Central Japan Railway Company (JR Tokai) at our Mie Plant. Through interacting with another company at safety and health exchange meetings, we are working to improve the level of safety and health of both companies.
In addition, employees belonging to the Safety and Health Section of the Onomichi Plant received the Green Cross Award at the National Industrial Safety and Health Convention held in October 2019. The award was presented to them in recognition of their daily efforts in health and safety activities.
In February 2020, a "Safety Personnel Meeting" was held at the Mishima Plant. Representatives from each plant in Japan and people involved gathered to participate in a lively question and answer session on safety measures.
In addition, employees belonging to the Safety and Health Section of the Onomichi Plant received the Green Cross Award at the National Industrial Safety and Health Convention held in October 2019. The award was presented to them in recognition of their daily efforts in health and safety activities.
In February 2020, a "Safety Personnel Meeting" was held at the Mishima Plant. Representatives from each plant in Japan and people involved gathered to participate in a lively question and answer session on safety measures.
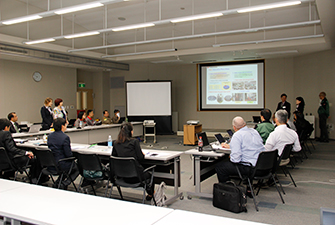
Announcements on safety activities by employees from each plant
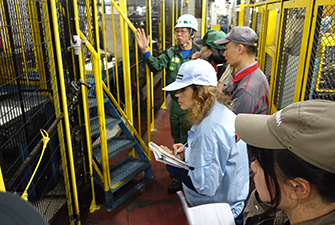
Observed equipment safety measures
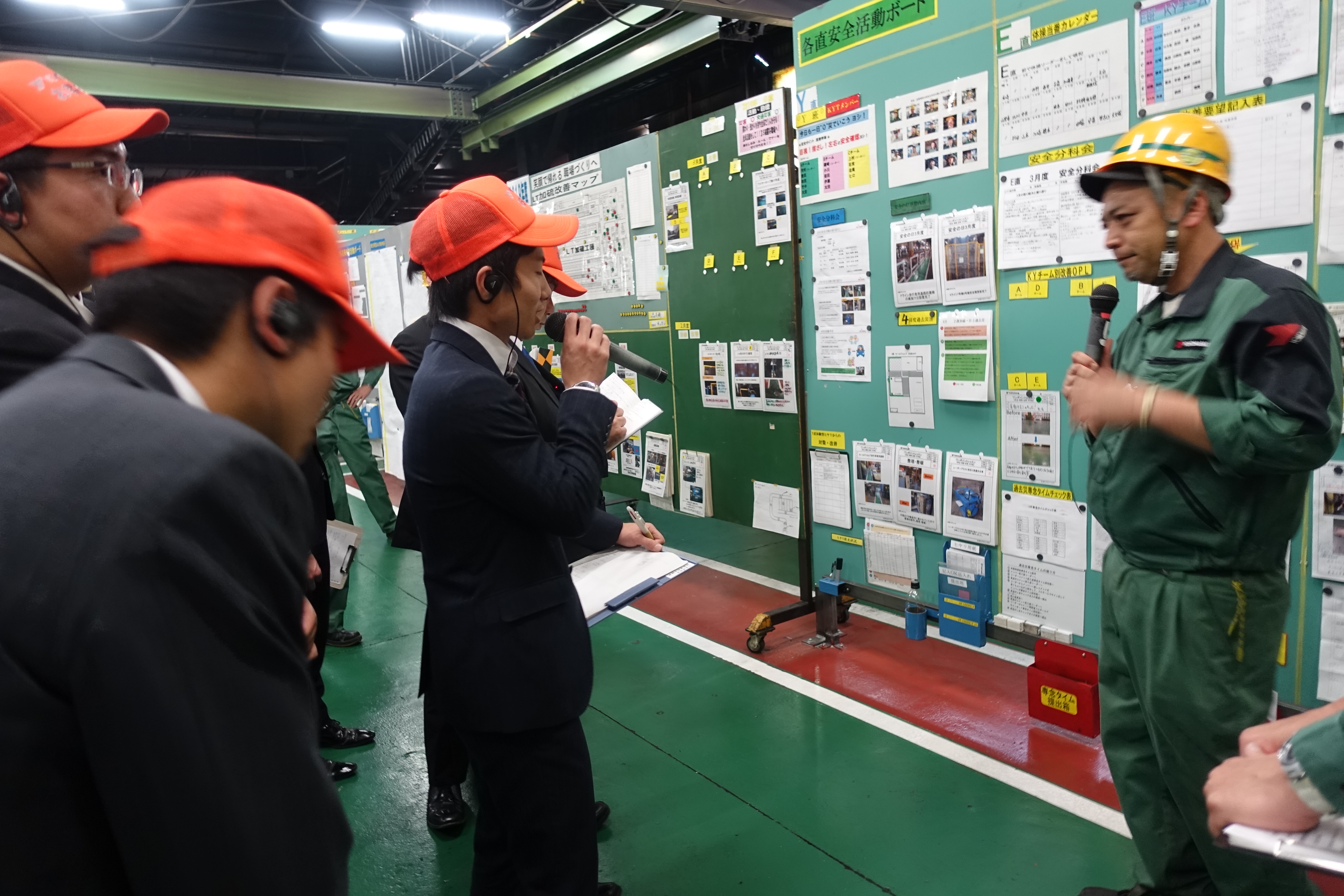
JR Tokai exchange meeting
Future challenges
We are implementing various measures aimed at creating a safe and employee-friendly workplace environment, and at safeguarding employees’ health; however, the current situation is that we have yet to realize our goal of reducing the number of accidents to zero.
Besides proceeding with equipment-related measures that focus on maintaining distance from sources of danger, we are also working to cultivate employees who know how to act safely.
Besides proceeding with equipment-related measures that focus on maintaining distance from sources of danger, we are also working to cultivate employees who know how to act safely.