The Environment
Materials
KPI
Move the screen to the left or right to see the table information
Item | FY 2021 results | FY 2022 results |
---|---|---|
Total volume of raw materials used | (Consolidated) 1,068,000 tons | (Consolidated) 1,088,000 tons |
Ratio of renewable/recycled raw material | (Consolidated) 25.5% | (Consolidated) 26.2% |
Responsible Departments
Technology and design departments
- Supervised by the 4Rs Committee
Our position and Targets
Why are “Materials” a critical issue for us to address?
Explanation of the reason and background
The Yokohama Rubber Group sells products using both natural and chemically composed materials including natural rubber and water. All of these materials are made from resources available on our planet, which are by no means infinite. Therefore, we believe that it is important that we should address the challenges of delivering products that will please customers and society, while minimizing material usage, promoting the sales of recycled products (such as retread tires), and using renewable or recycled materials whenever possible.
Our policy and position relating to raw materials
The Yokohama Rubber Group has presented its environmental philosophy in the "Yokohama Rubber Basic Environmental Policy" and "Yokohama Rubber Environmental Policy", will work to develop and procure raw materials in a manner that reduces environmental impacts and minimizes material usage in accordance with the "Yokohama Rubber Group Action Guidelines".
Vision and targets
Long-term target: 100% sustainable raw materials usage by 2050
Mid-term target: At least 30% renewable/recycled raw material usage by 2030
Mid-term target: At least 30% renewable/recycled raw material usage by 2030
Measures to pursue our vision
We promote the development and use of raw materials that have least impact on the environment and society through the following initiatives in order to continue our business.
We also have a system to procure sustainably-available raw materials that will have the lowest environmental and social impacts throughout their life cycles.
We also have a system to procure sustainably-available raw materials that will have the lowest environmental and social impacts throughout their life cycles.
- We review factors such as structural design and material rigidity to fulfill the required performance while achieving weight reductions.
- We promote the sales of retread tires.
- We explore and utilize innovative recycled and renewable materials, while further increasing the use of existing recycled and renewable materials.
Review of FY 2022 Activities
Expanding the use of renewable raw materials toward a recycling-oriented society
We have long been promoting the use of renewable and recycled raw materials as part of our efforts to realize a recycling-oriented circular economy. In addition to the use of recycled rubber, which we have been actively working on, we are now expanding the use of a wider variety of recycled and renewable raw materials, including wires made by melting and reusing scrap iron, silica made from plant-derived and inedible rice husks, and resins derived from natural materials.
In 2022, we used 273,000 tons of renewable raw materials worldwide, which accounts for 26.2% of our total raw material usage.
Toward realizing a renewable raw materials use rate of 30% in 2030, we explore and utilize innovative recycled and renewable raw materials, while further increasing the use rate of existing recycled and renewable raw materials, with the aim of solving environmental challenges our planet is facing.
In 2022, we used 273,000 tons of renewable raw materials worldwide, which accounts for 26.2% of our total raw material usage.
Toward realizing a renewable raw materials use rate of 30% in 2030, we explore and utilize innovative recycled and renewable raw materials, while further increasing the use rate of existing recycled and renewable raw materials, with the aim of solving environmental challenges our planet is facing.
The joint initiative by ZEON Corporation and us titled "Development of Manufacturing Technology for Synthetic Rubber Core Chemicals with Carbon Resource Recycling" has been adopted by NEDO as a "Green Innovation Fund Project / Development of Manufacturing Technology for Plastic Raw Materials Using CO2, etc." The Green Innovation Fund Project is a program established by the Ministry of Economy, Trade and Industry (METI) to accelerate innovation through structural transformation of energy and industrial sectors and bold investment toward achieving the national goal of "reducing overall greenhouse gas emissions to zero by 2050." The program provides a continuous ten-year support to companies and organizations that pursue this goal as a business commitment in the areas from research and development, demonstration to commercial implementation. Our demonstration project aims to establish two advanced technologies to produce butadiene and isoprene, which are key synthetic rubber chemicals based on carbon resource recycling, from renewable carbon resources such as used tires and biomass at high yield rates, with a view to commercially implementing them in the 2030s. This will contribute to the improvement of resource recycling and carbon neutrality in the tire and rubber industries.
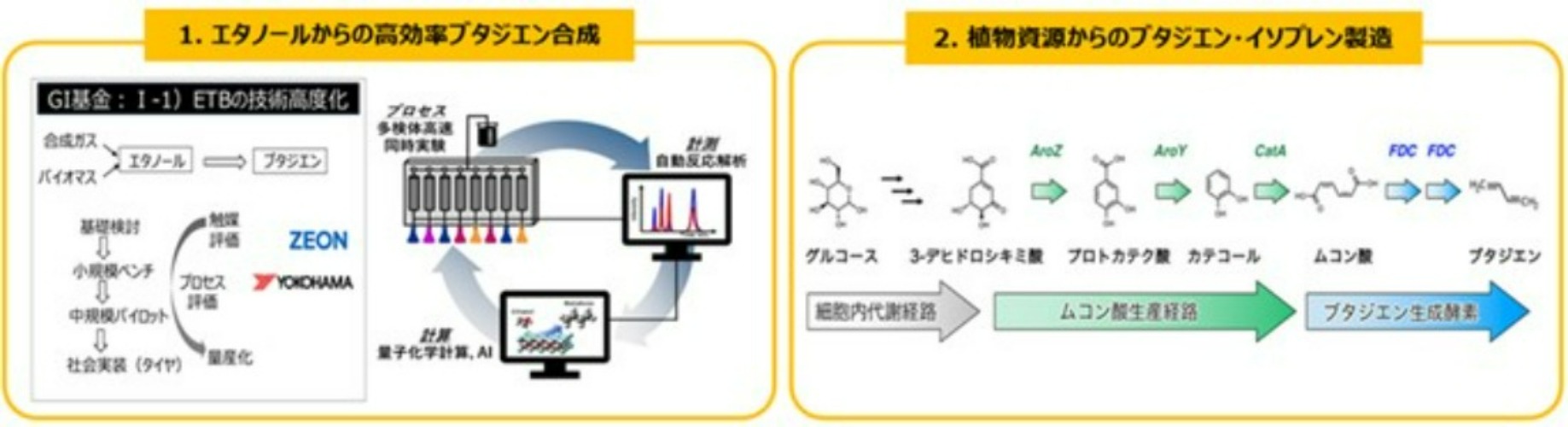
Outline of the Project for Development and Demonstration of Carbon-Resource-Recirculating Synthetic Rubber Core Chemicals Manufacturing Technology
Yokohama Rubber to join a tough hill climb race in the U.S. with tires made from sustainable materials for the firs time
Yokohama Tire Corporation, our tire sales arm in the United States, supported 23 cars in the "100th Pikes Peak International Hill Crime" held in Colorado, U.S. on June 26, 2022, supplying "ADVAN A052" street sport tires made from sustainable materials for the first time. This is a traditional hill climb competition that has been held since 1916, also known as the "Race to the Clouds," which starts at an elevation of 2,862m and covers 20km before finishing at an altitude of 4,300m.
Among the cars supported by Yokohama Rubber, the "ADVAN A052" tires made from sustainable materials were used on the "Electric Performance/NRS 2022 Tesla Model S Plaid" piloted by Blake Fuller, competing in the Exhibition Class. These ADVAN A052 tires have a more recyclable material composition than their previous version, where the sidewall rubber material, which is subject to most severe deformation during vehicle travel, has been changed from the conventional petroleum-derived butadiene rubber to a biomass-derived butadiene rubber. Blake Fuller finished the competition in the sixth place in the class he competed in.
Actually, competing in this harsh hill climb event has provided us with new knowledge and will further accelerate our development of technologies that will reduce tires’ burden on the environment. We will continue to work on the development of tires featuring sustainable materials.
Among the cars supported by Yokohama Rubber, the "ADVAN A052" tires made from sustainable materials were used on the "Electric Performance/NRS 2022 Tesla Model S Plaid" piloted by Blake Fuller, competing in the Exhibition Class. These ADVAN A052 tires have a more recyclable material composition than their previous version, where the sidewall rubber material, which is subject to most severe deformation during vehicle travel, has been changed from the conventional petroleum-derived butadiene rubber to a biomass-derived butadiene rubber. Blake Fuller finished the competition in the sixth place in the class he competed in.
Actually, competing in this harsh hill climb event has provided us with new knowledge and will further accelerate our development of technologies that will reduce tires’ burden on the environment. We will continue to work on the development of tires featuring sustainable materials.
Recycling activities in the MB business
Similarly, to the previous year, recycled rubber was mainly used for ballast belts with its use rate being 2.6% by weight in FY2022. We are also working to promote the adoption of recycled carbon and rubber raw materials recycled from waste tires and other rubber waste.
The plastic mold material used in the hose manufacturing process, which are thermoplastic resins, are crushed and re-melted for reuse. However, the powder generated in the crushing process used to be discarded as waste. To address this issue, we now have a highly controlled two-stage crushing process, of which first stage yields crushed particles with much larger diameters than fine powder that quickly scatters.
The finer powder generated in the second crushing stage is collected and reused, carrying the traceability information as that of the main crushed resin.
The plastic mold material used in the hose manufacturing process, which are thermoplastic resins, are crushed and re-melted for reuse. However, the powder generated in the crushing process used to be discarded as waste. To address this issue, we now have a highly controlled two-stage crushing process, of which first stage yields crushed particles with much larger diameters than fine powder that quickly scatters.
The finer powder generated in the second crushing stage is collected and reused, carrying the traceability information as that of the main crushed resin.
Yokohama Rubber Nagano Plant receives the "Japan Environmental Management Association for Industry (JEMAI) Chairman's Award" for its metal scrap briquetting
We received the "JEMAI Chairman’s Award" for our metal scrap briquetting technique at the "Resource Recycling Technologies and Systems Awards" in 2018.
The Nagano Plant produces joint fittings for hoses and assembles hoses and fittings. The plant has developed an effective system to contribute to better resource recycling, in which the metal scraps generated during the production of metal fittings, that used to be sold to external metal scrap suppliers, are shaped into briquettes that can be used for steel production by applying massive pressure that allows forming the scraps in any designed shape so that they can be directly sold to steel manufacturers.
The Nagano Plant produces joint fittings for hoses and assembles hoses and fittings. The plant has developed an effective system to contribute to better resource recycling, in which the metal scraps generated during the production of metal fittings, that used to be sold to external metal scrap suppliers, are shaped into briquettes that can be used for steel production by applying massive pressure that allows forming the scraps in any designed shape so that they can be directly sold to steel manufacturers.
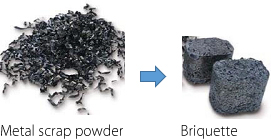
Future challenges
While using raw materials in business activities is unavoidable, our final goal is to be in a state which minimizes the use of the resources available on our planet.
A key issue is correctly assessing whether the use of reusable products and recycled materials actually results in a reduction in the use of the planet’s resources and the environmental impact, and deploying the technique on a global level if found effective.
A key issue is correctly assessing whether the use of reusable products and recycled materials actually results in a reduction in the use of the planet’s resources and the environmental impact, and deploying the technique on a global level if found effective.