Get Back ADVAN
手を取りあう、伝統と革新―
横浜ゴム 新城工場に貫かれた情熱。
/ 前編
2021.12.25
ADVANブランドを含めた横浜ゴムの高性能タイヤは、いったいどのように生産されているのか。半世紀以上の歴史を持ちながら、時代ごと常に最先端工場として成長を続けてきた横浜ゴム 新城工場に潜入した。そこには、圧巻のオートメーション設備と、そしてタイヤづくりにかける職人の魂があった。
Words:中三川大地 / Daichi Nakamigawa Photography:安井宏充 / Hiromitsu Yasui
横浜ゴム 新城工場 / 前編
ハイパフォーマンスタイヤを生み出す
最新鋭のオートメーションマシン。
それは、ひとつのゴムの塊が、我々にとって馴染みのある、安心して命を預けられる“タイヤ”になった瞬間だった。
ずらりと並んだこの加工機はブラダーと呼ばれている。ゴム風船状の圧縮装置を使って高温、高圧で“ゴムの塊”を押し付ける。するとゴムと硫黄の分子が結合し、はじめてゴムに弾力性と耐久性が生まれる。また、タイヤにとっての大切な“表情”となるトレッドパターンやサイドウォールのロゴも、この時、しっかりと刻まれていく。これら一連の工程は、加硫工程と呼ばれている。まさにタイヤが産声をあげるかのようなシーンである。
タイヤが“産声”を上げた瞬間。ブラダーと呼ばれるゴム風船状の圧縮装置を使って高温、高圧で“ゴムの塊”を押し付ける。ゴムと硫黄の分子が結合し、はじめてゴムに弾力性と耐久性が生まれる。トレッドパターンやサイドウォールのロゴもここで刻まれていく。
横浜ゴム 新城工場。ここはADVANブランドを筆頭とした、同社の主軸となるタイヤ製品を生産する最先端工場として稼働している。1964年に操業して、いち早くスチールラジアルタイヤの生産を開始したという歴史のある工場だ。
しかし、半世紀以上の歴史を持つからといって、決して旧態然としたインフラではない。事あるたびに新技術を取り入れ設備を増強し、多品種生産への対応を図ってきた。母体となる新城工場のほか、2000年代には新城南工場も稼働を始め、のべ敷地面積はおよそ33万1000㎡へ。そこで約1200名のスタッフが従事する、国内最大規模のタイヤ生産拠点となった。つまり、ADVANブランドを含む、横浜ゴムの幅あるラインナップのタイヤ生産に欠かせない屋台骨である。
冒頭では加硫工程に入る際の素材を、抽象的なイメージとして“ゴムの塊”と記したが、実際にはブラダーに送り込まれる段階で、すでにいくつもの工程を経ている。トレッドパターンのないドーナツ状のゴムは、グリーンタイヤ(生タイヤ)と言われる。
ゴムにあらゆる原材料を加える混合工程にはじまり、ビードやカーカス、ベルト部をつくる材料加工工程、それをドーナツ状のグリーンタイヤとしてまとめる成形工程を経て、冒頭の加硫工程へと行きつく。
ビードやカーカス、ベルト部をつくる材料加工工程を経て、ドーナツ状のグリーンタイヤとしてまとめていく成形工程へと入る。徐々にタイヤの形へと近づいていくのがわかる。
工場の規模に対して、従事する人員は意外なほど少ない。ほぼオートメーション化されているからだ。我々が見たのは、2017年に新設したばかりという最新鋭のラインだったという理由もある。それはグリーンタイヤを生み出す成形工程と呼ばれるところだった。
タイヤカタログの技術解説を見るとわかるように、タイヤは単にゴムの塊ではなく、その内側にはカーカス、ベルト、ビード部などを重ねた複数の層になっている。バラバラに生産されるそれらの部材を、タイヤのかたちに組み上げるのが成形工程である。
1本のタイヤをつくるのに必要な部材は、緻密な生産計画に基づいて、必要な分だけ成形する工作機械へと投入される。成形工程で使われる巨大な工作機械を動かすのは、オペレーター、材料を運ぶ人や材料を交換する人(サプライヤー)、そして管理者など、ごく数名しかいない。少数精鋭ながらも一致団結し、膨大な量のグリーンタイヤを加硫工程へと送り届けている。
「無駄な在庫を持たず、必要な時に必要な量だけ生産するというのが工場のポリシーです。そのほうがお客様の欲するものが、迅速に届けられるからです。なによりもゴムは生き物。鮮度が命だと言われています。特に生ゴムは温度や湿度などの環境によって、すぐに伸縮や硬化が始まります。加工する前の状態を短く済ませる生産体制は非常に理にかなっています」
この日、我々を案内してくれた新城工場の業務課 課長・廣川一八(ひろかわ・かずや)の「ゴムは生き物」という表現が非常に印象的であった。
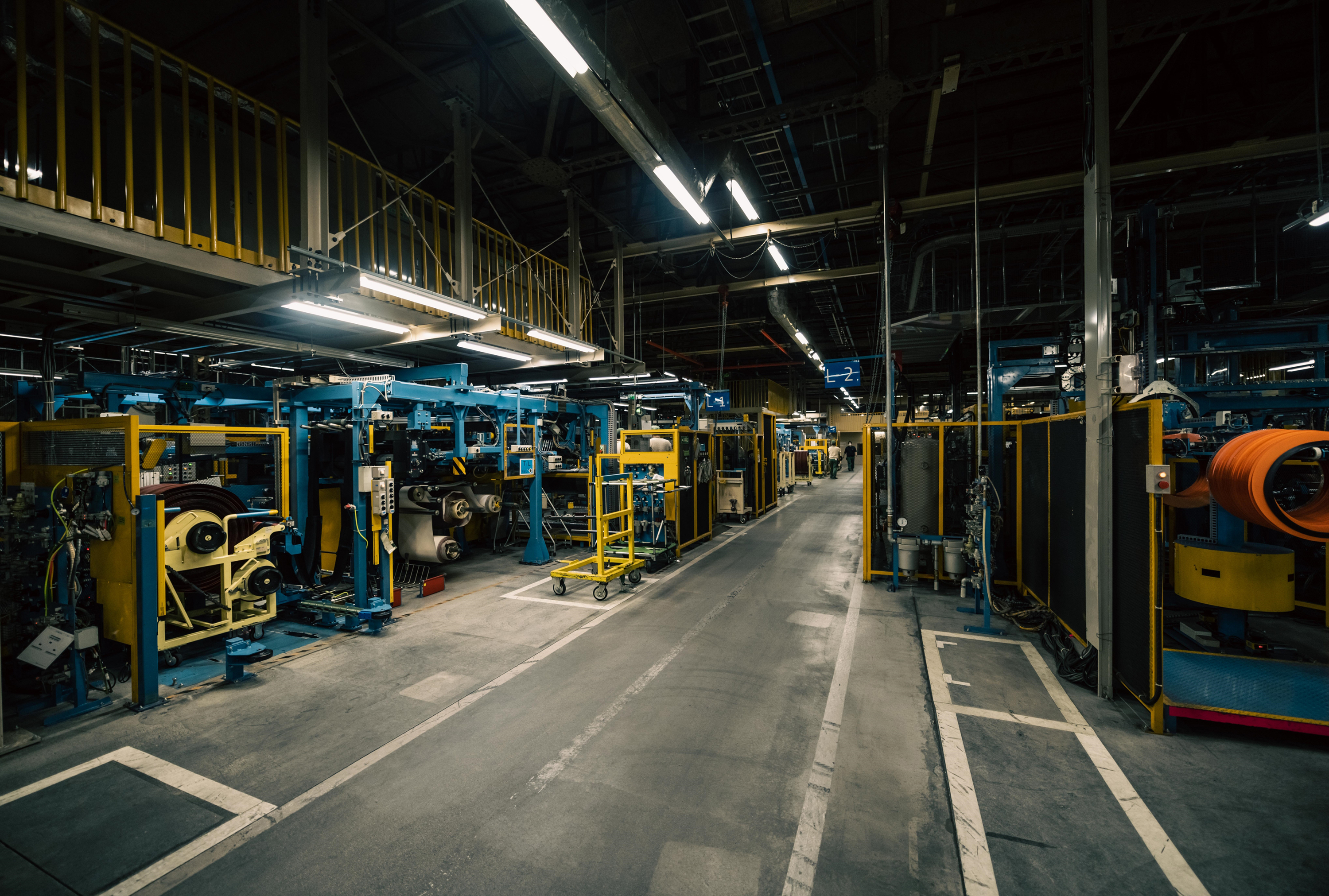
2017年に新設されたグリーンタイヤを生み出す成形工程のライン。最新鋭の技術でオートメーション化され、その規模に対して働く人員の数は効率的に精鋭化されている。温度や湿度などの環境によって伸縮や硬化に影響が出やすい生ゴムには、“鮮度”を保つ上でも加工する前の時間を短く済ませる効率的な生産体制が求められる。
機械を決して過信してはいけない。
モノづくりの主役は人間である。
彼らはオートメーションだからといって機械任せにせず、少しも気を抜くことがない。生産するタイヤの銘柄やサイズが変われば、その都度、材料やプログラムを変更する必要がある。
最新鋭の技術を信頼しているといっても、適切に成形されているか、不良品はないか、1本ずつ人間の目と指先でていねいに見極めていたことも印象に残る。特に平坦な素材をつなぎ合わせて円形にする工程は、誰もが細心の注意を払って見守り、みずからの手先で確認をしていた。
取材、撮影の際の廣川課長からの注意事項を思い出した。「オートメーション化されたライン内に身体を入れてしまうと、センサーが作動して瞬時にラインが止まるので注意してください」と、説明を受けたのだった。それを遵守したことを現場で伝えると彼はこう言った。
「従業員の安全を守ることが第一ですが、決してそれだけではないのです。特に操作をすることなく、作業者が足を踏み入れるだけで機械の動きが止まれば、自分が入りたい時に入れる。逐一、品質を見ていられるし、手直しができる環境です」
機械に支配されてはいけない。機械はあくまで、優れた製品をつくるための道具だと思った。
「瞬時のジャッジですかね。目と指先の感覚と。部材のつなぎ合わせには規格があり、なおかつSOP(標準作業手順書)によって、我々の作業は規定されています。それでも、たとえ1本でもイレギュラーが出ないとは限らない。その時に規格内に収まるように、どう処理するか。そういうものは経験のなかで覚えながら、見ていかなければならない」
彼らはいかに優れたインフラを持つからといって、いい意味で「機械を信用していない」のだった。オートメーション設備をオペレーションしながらも、必ず自分たちの目と感触での“納得”を欲していた。不良品だったと笑って済まされない、命に直結する製品を扱っているという自負を誰もが持っていたことの象徴である。
帽子の横に黄色いラインが入るのが作業長や技師の証。オートメーション化されたラインであるからこそ、常に人の目で工程に異常がないかを見回る“重点管理”が実施されている。いかに優れたインフラを構築しようとも、機械を信用し過ぎない。あくまでタイヤは“人”によってつくられていることを実感する光景だった。
それは加硫工程を経たのちの検査工程にもあらわれていた。仮想走行状態に持ち込んでのバランス測定やユニフォーミティ(タイヤの均一性)測定、さらにはX線検査など。先進的な機器によって、あらゆる検査が実施される。もちろん、抜き打ちではなく、1本ずつ確実に実施されるのは言うまでもない。
それでも最後はやはり、人間の目と指先で、最終検査が実施されている。社内での訓練を受けて認定を得た人間だけが、最終検査に携わることができるという。この手を離れたら、いよいよ製品としてユーザーのもとへ届けられる。常に身の引き締まる思いで、彼らはタイヤと向き合っている。
先進的な機器による検査工程を経たのち、ここでも人間の“目”と“感触”による最終検査が行われる。これはADVAN Sportの最新鋭グローバルフラッグシップタイヤである「V107」の最終検査の様子。どんなに最新鋭の機器を投じたオートメーションな工程であっても、最後は必ず人の手が入るところに、横浜ゴム 新城工場のものつくりに対する誠意ある姿勢を感じる。
技術は一日にしてならず。
歴史に裏打ちされた職人の哲学。
ADVAN Sport V107が遂に発表された。下は18インチから上は23インチまで、偏平率の低い、攻めた設定まで網羅される。しかも、サイズによっては300km/h以上の高速走行を許容し、大型SUVを受け止める耐荷重性能を満足させなければならない。それを成し遂げたエンジニアリングの進化には感服させられる。と、同時に生産現場もそこに立ち向かっていることを知った。
最新鋭のオートメーション工場といえば、人間不在でまかりとおる、ドライな生産現場を思い浮かべてしまう。しかし、横浜ゴム新城工場は、どこまでいっても人の能力を大事にしていた。
いかに最先端のタイヤ開発能力や、生産インフラがあるからといって、一朝一夕で高性能タイヤができるわけではない。機械はあくまで道具に過ぎない。横浜ゴム新城工場が半世紀以上かけて蓄積したノウハウがあってはじめて、それら設備や設計が活きてくるのだと思えた。そこに欠かすことのできない財産は“人”だった。職人といってもいい。
そう思い至ってから、あらためて世に送り出されることを認められた完成品としてのタイヤを見る。それはまるで、芸術作品が世界に向けて羽ばたく瞬間を見たようだった。工場で働く一人ひとりの想いが、まぎれもなくここに結実していた。
(文中敬称略)
横浜ゴム 新城工場 / 前編
いいね
横浜ゴム株式会社
新城工場
横浜ゴム 新城工場はADVANブランドを筆頭とした、同社の主軸となるタイヤ製品を生産する最先端工場として稼働している。その操業は1964年。いち早くスチールラジアルタイヤの生産を開始したという歴史のある工場ではあるが、時代の要請に合わせて常に新技術を取り入れ設備を増強し、多品種生産への対応を図ってきた。母体となる新城工場のほか、2000年代には新城南工場も稼働開始。のべ敷地面積はおよそ33万1000㎡と国内最大級の生産工場となった。従業員数は約1200名。横浜ゴムの幅のあるラインナップのタイヤ生産に欠かせない屋台骨である。
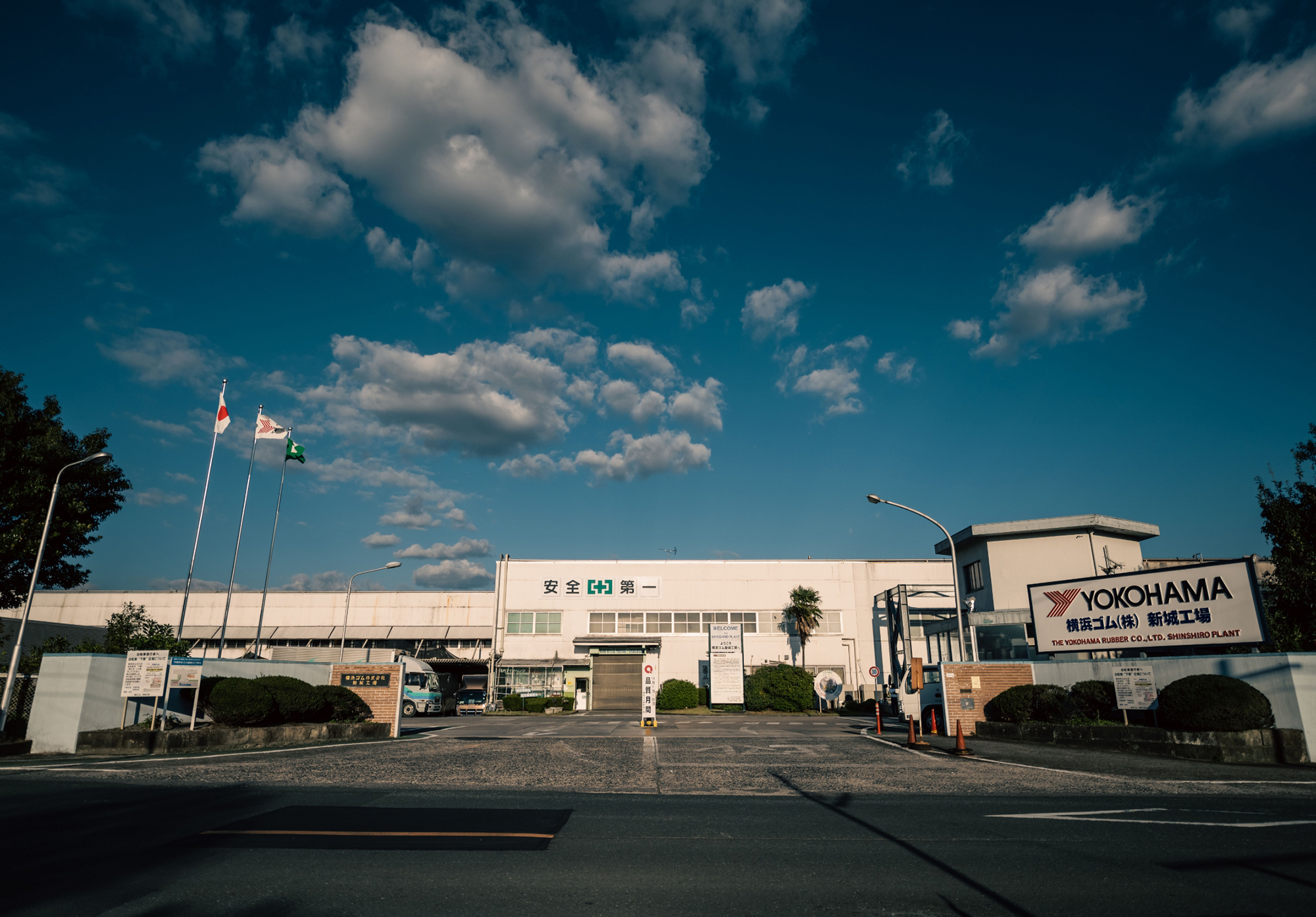