Get Back ADVAN
手を取りあう、伝統と革新―
横浜ゴム 新城工場に貫かれた情熱。
/ 後編
2022.1.7
最新鋭の設備と、職人魂が同居する横浜ゴム新城工場では、誰もが情熱を持ってタイヤ生産に取り組んでいた。決して機械任せにすることなく、誰もが技術習得に熱心で、心底から「品質、安全、環境」と向き合ってきた。かねてよりタイヤ生産に従事してきた、ふたりの職人の言葉を紹介する。
Words:中三川大地 / Daichi Nakamigawa Photography:安井宏充 / Hiromitsu Yasui
タイヤにとっての“品質”とは
お客様の安全に直結するもの。
我々が考えうるなかで、タイヤはもっとも過酷な条件にさらされるゴム製品だ。何トンもの重さを支えながら高速回転し、一切のフラつきも生じさせず、あらゆる環境下の路面を捉えていかなければならない。さらに消費者の欲望は果てしない。快適な乗り味が求められ、なおかつ長期的な耐久性やコストへの要求も厳しい。なにより、万が一にでもそこに製品不良があっては、命の危険に直結する。横浜ゴム新城工場で働く職人たちは、誰もがそれを自らに戒めて作業する。
「品質とはなにか。安全とはなにか。若いころに上司から口を酸っぱくして言われてきました」
前編で取り上げた成形工程の、その職長を務める大久保龍嗣(おおくぼ・りゅうじ)は述べる。彼は18歳で就職してから20年ほど、ずっとタイヤ生産一筋で生きてきた職人だ。あらゆる工程をわたり歩き、その上で品質技師も経験し、現在は現場を統括するような立場である。
「どんなにパワーがあるクルマでも、高級車であっても、タイヤがなければ走れない。それだけ重要なものをつくっているという認識がまず必要です。しかもタイヤにトラブルが生じれば、時に命にかかわるほどの危険な状態になる。タイヤにとっての品質とは、あらゆる製品以上にお客様の安全に直結するものだということ。そのために厳格に定められた規格があり、守るべきルールがある。けれども、ただ決められたマニュアルをこなすだけではない。誰もが指先の感触でわかるくらい、素材や製品のことを熟知しているし、何かあればすぐに会社に対して改善案を出す。品質は工場責任者やタイヤ開発者だけが考えることではなくて、工場で働く誰もが突き詰めていかなければならない」
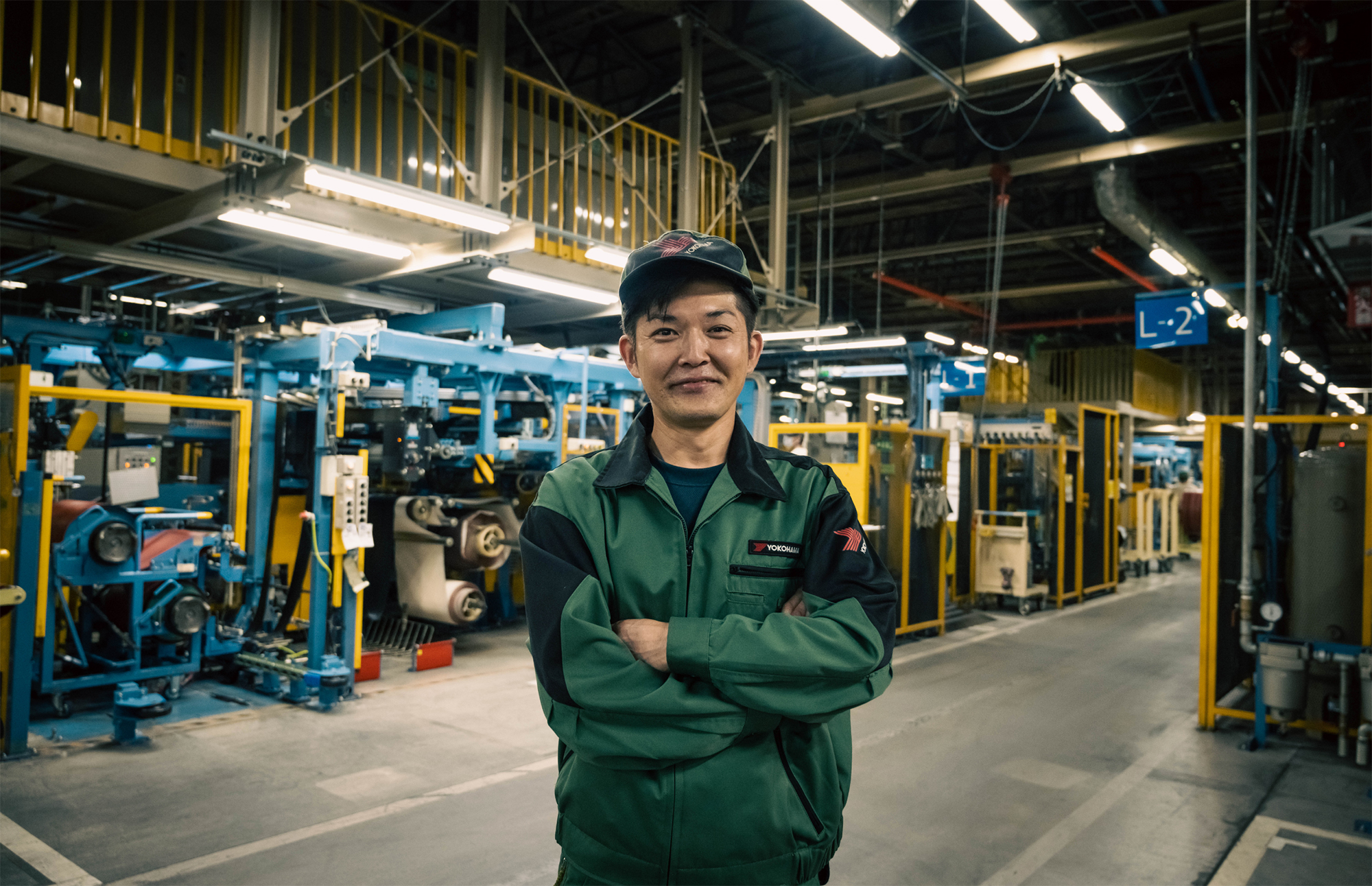
成形工程の職長を務める大久保龍嗣。18歳で就職してから一貫して横浜ゴム 新城工場で従事してきた職人である。多くがオートメーション化された現代のラインはどこか無機質な冷たさを感じるかもしれないが、この大久保の表情のとおり、それを動かしている人間たちの中には熱い情熱と、何より“YOKOHAMA”製品に対する誇りが貫かれている。
我々は機械を操る仕事をしていない。
“タイヤをつくる”仕事をしている。
先に取り上げた成形工程は、その多くがオートメーション化されている。だからと言って機械任せでいいはずがなく、常に人間の目と手を動かして確認することが必要だと述べた。
「ボクらは材料を運んだり、ボタンを操作する仕事をしているのではない。“タイヤをつくる”仕事をしているんです。モニターの見方やボタンの押し方を覚えるのではなくて、“タイヤのつくり方”を覚えなければならない。ボタンを押せば、あらゆる作業を自動的にやってくれる。それは効率的だと思います。でも人間に代わって機械が何をしてくれたのか、というのを理解する必要があると思います。そうでなければ真の意味でのオペレーションはできないし、万が一の際に補正をすることもできない」
最新鋭のオートメーションシステムは、誰でも動かせると思いきや、しかしそこに従事する人間の見かたは違っていた。機械が何をしているのかわからなければ、決して満足のいくオペレーションはできないと断言する。逆に言うと手作業でタイヤをつくってきた人間にとって、最新鋭のオートメーション設備は、このうえなく効率的な現場であると理解するようにもなった。
「いきなりここで働けと言われても、最初は何が何だかわからないと思います」
そう話すのは、成形工程でビルダーとして働く伊東九樂(いとう・くらく)だった。彼は横浜ゴム新城工場に入社して6年ほど。当初は別の生産現場にいたという。先に触れたオートメーション工程とはまた別の、昔ながらのアナログな生産現場である。タイヤの生産工程こそ同じだが、それに伴う作業の多くが手作業だ。自分で材料を切って、運んで、工作機械に投入して、と。あらゆる工程を自分の手で扱う必要がある。もちろん、生産効率の面ではオートメーションに敵わない。しかし、こうしたインフラも新城工場はたいせつに守り続けてきた。それが生産規模を支えることにつながるだけでなく、“タイヤのつくり方”を学ぶ現場としても機能しているようだった。
「この現場に来て1年半ほど。この迅速で効率的な機械のスピードに合わせようとすると、最初は難しいし、慣れないこともありました。でも今思えば、タイヤの構造を、そしてつくり方のノウハウを知ってはじめて、このオートメーションをオペレーションできるようになるのだと思いました。機械が何をしているのかを自分自身が理解すれば、絶対に人が確認したほうがいいところもわかります」
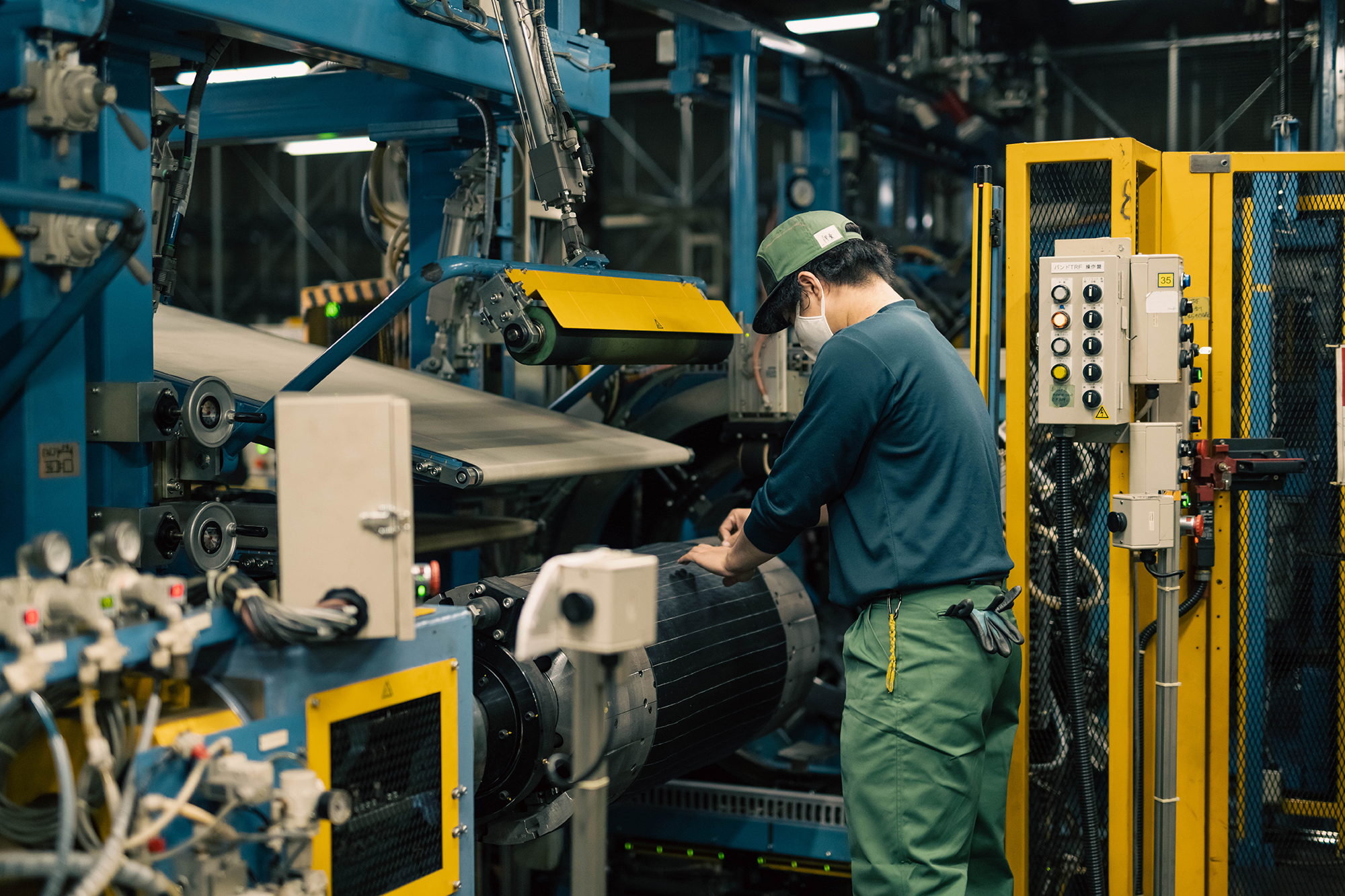
成形工程でビルダーとして働く伊東九樂。横浜ゴム新城工場に入社して6年経つが、現在の持ち場に就いたのは1年半ほど前で、それまではよりアナログな生産現場でタイヤづくりの基礎を学んだのだという。多くを“手作業”で経験し、タイヤづくりのノウハウを理解できたことが、現在のより効率的なオートメーションによる製造ラインのオペレーションに大きく役立っているという。
“ADVAN”を創っていることを
ここで働く誰もが誇りに思っている。
そんな伊東と同じ道を、大久保もたどってきた。まだ今よりもはるかにアナログな時代で、オートメーション設備もない。そんな環境下で悪戦苦闘し、タイヤづくりを学んできた。
「大きな志を抱いて入社したわけではありません。当時は手作業に頼る工程が多くて、手がボロボロになったり、残業も多かったり。そんななかで上司に怒られたりもして。それでも品質、安全、環境のことを考え、特に“お客様の安全を支えている”という意識を持って食らいついてきました」
そんな大久保はクルマが大好きだ。ADVAN HFタイプDを履いたクラシック・ミニでサーキットを走ったりしながら、ADVANの性能を体感してきた。 Neovaを履いて、足しげくサーキットやジムカーナに通う部下もいる。そうしたカルチャーの中で“タイヤ評価”にまつわる雑談は世界中で見受けられる光景だが、その素材自体をみずからこの場所で生み出していることを、彼は誇りに思っていた。
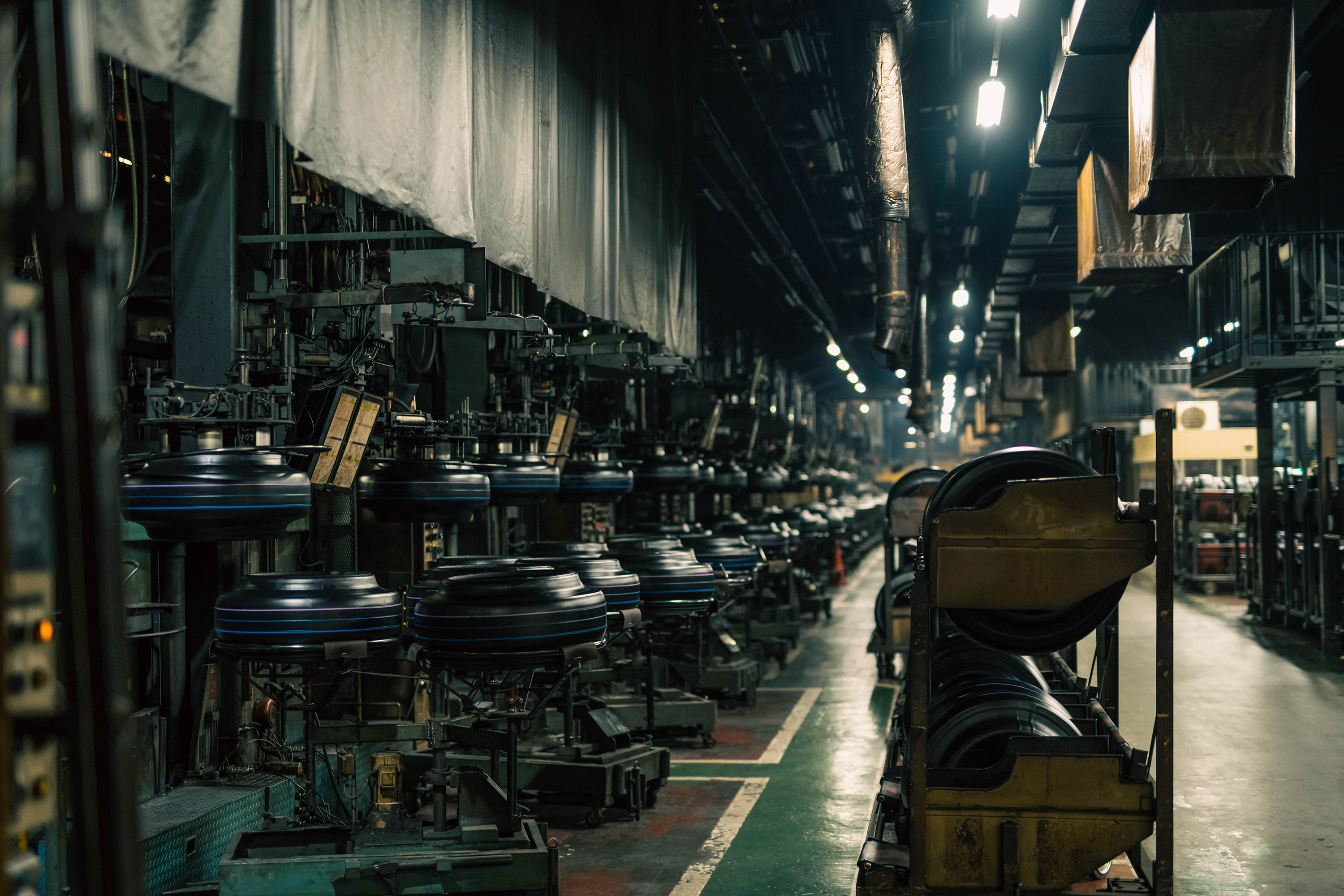
1964年に操業した横浜ゴム 新城工場は、時代に併せた進化と変革を常に遂げてきたが、現在も一部でアナログな時代の名残を感じさせる製造ラインが残されている。オートメーション化の波は進行しているが、こうしたアナログな世界を経験することで、現代の効率的な製造工程をより深く幅のある視点から俯瞰できることも確かである。
いや、たとえスポーツカーに乗っていなくても、モータースポーツに興味がなくても、ADVANブランドはここに従事する誰もが知っている。大谷翔平選手がホームランを打ったとき、「YOKOHAMA」の看板が映ることを誰もが願っている。幹線道路を走っていてADVANの看板を掲げたタイヤ販売店を見つけたら、どこか誇らしげな気持ちになる。
「信号待ちで隣にクルマが並ぶと、いつもサイドウォールを見ていますね。ADVANを履いていてくれたら、めっちゃ嬉しくなります」
と、彼らは無邪気に笑う。それは自分たちがつくったタイヤに絶対的な自信を持ち、己の作品をちょっぴり自慢したい気持ちと似ているのかもしれない。そうした感情を、製品企画者や設計開発者、あるいはテストドライバーが抱くのは自然かもしれない。だが、ここでは生産に携わるその誰もが、そのプライドを持っていたのがとても印象的だった。
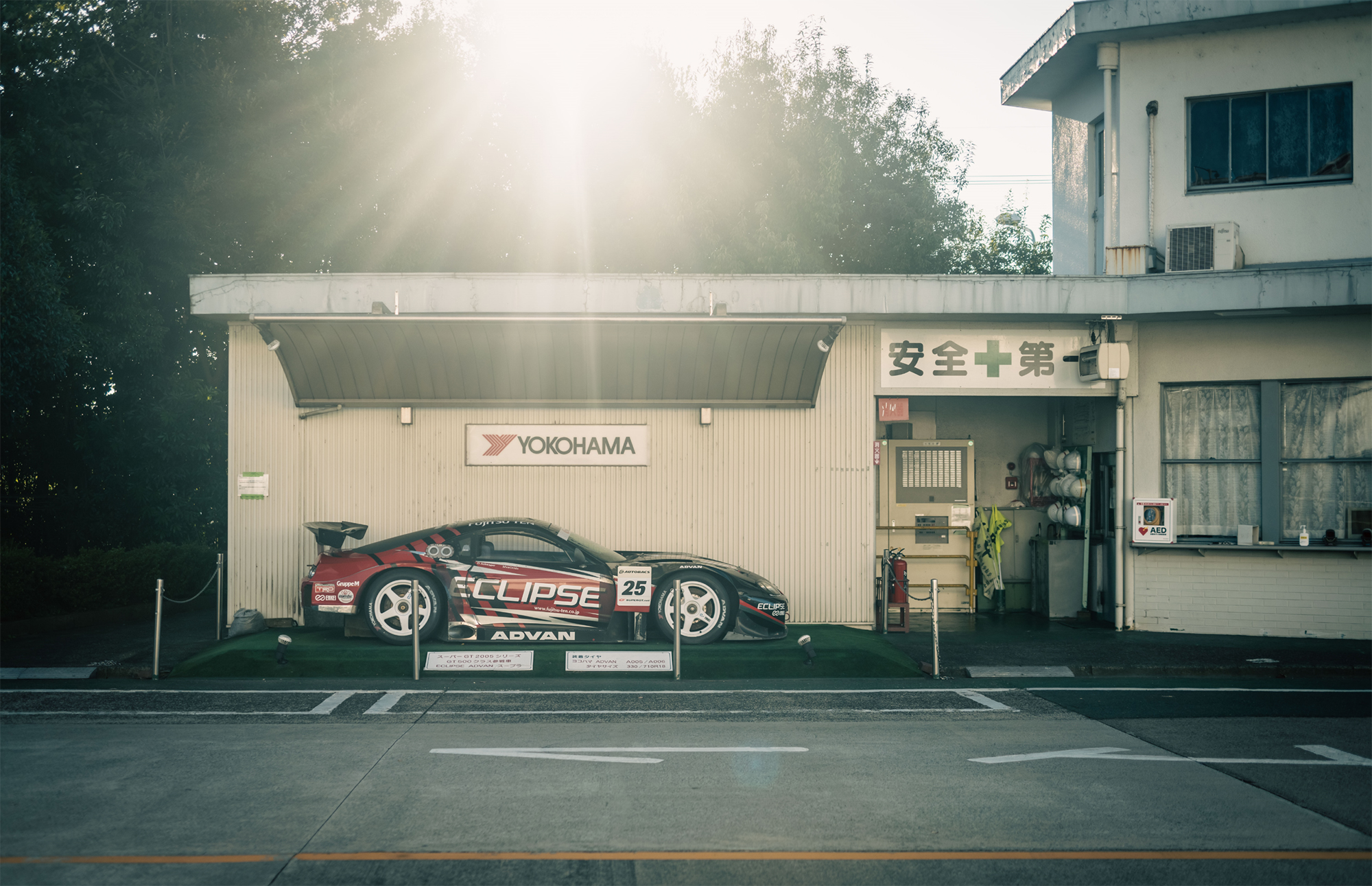
“SUPER GT元年”となった2005年のSUPER GT第1戦・岡山で、GT500クラス優勝を遂げた#25 ECLIPSE ADVAN SUPRA(TEAM ADVANツチヤ)は現在、横浜ゴム株式会社新城工場の入口に展示されている。YOKOHAMA/ADVANらしい“熱いスピリット”を象徴するマシンが、毎日工場に出勤する従業員たちの姿を見守ってくれている。
いかに技術が進化し、オートメーションに代表される効率的な生産現場になったとしても、やはりタイヤは人がつくっている。ADVANを愛する者たちが、プログラムのスイッチを入れ、そして逐一見守り、時に手直しをしている。そう、そこにプライドという名の“魂”をこめながら。彼らがつくるタイヤには、だから全幅の信頼を持って命を預けられると思えた。
(文中敬称略)
いいね
横浜ゴム株式会社
新城工場
横浜ゴム 新城工場はADVANブランドを筆頭とした、同社の主軸となるタイヤ製品を生産する最先端工場として稼働している。その操業は1964年。いち早くスチールラジアルタイヤの生産を開始したという歴史のある工場ではあるが、時代の要請に合わせて常に新技術を取り入れ設備を増強し、多品種生産への対応を図ってきた。母体となる新城工場のほか、2000年代には新城南工場も稼働開始。のべ敷地面積はおよそ33万1000㎡と国内最大級の生産工場となった。従業員数は約1200名。横浜ゴムの幅のあるラインナップのタイヤ生産に欠かせない屋台骨である。
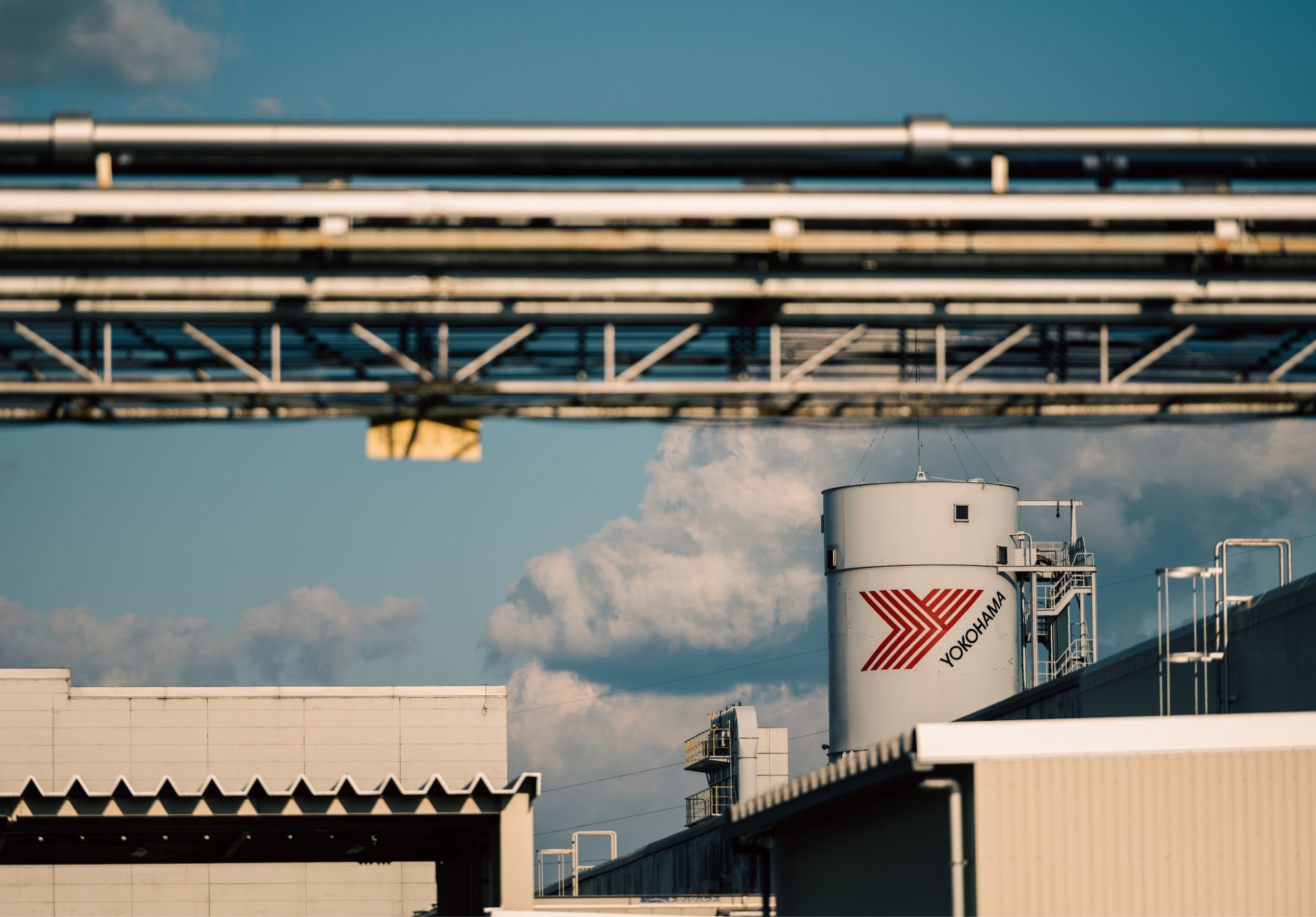