Consumer Issues
Customer Health and Safety
KPI
Responsible Departments
Our position and Targets
Review of FY 2022 Activities
Introduction of Initiatives
Future challenges
KPI
Move the screen to the left or right to see the table information
Item | FY 2021 results | FY 2022 results |
---|---|---|
Total number of violations of regulations and voluntary standards concerning product safety | (Consolidated) 1 | (Consolidated) 2 |
Implementation rate of product safety and evaluation (including determination based on compliance with design standards) based on review of design plan for tire products and MB products. | 100% | 100% |
Responsible Departments
Tire Quality Assurance Dept. (including related products)
Hose and Couplings Quality Assurance Dept. & Industrial Products Quality Assurance Dept. (products other than tires)
Monitoring by the Quality Audit Department from an internal third-party position
Hose and Couplings Quality Assurance Dept. & Industrial Products Quality Assurance Dept. (products other than tires)
Monitoring by the Quality Audit Department from an internal third-party position
Our position and Targets
Why is “Customer Health and Safety” a critical issue to be addressed?
Explanation of the reason and background
If there is a quality issue with tire products or MB products of the Yokohama Rubber Group, it could have a significant impact on the customer’s life, property, or environment. In order to achieve sustainable management, it is important to build credibility by having secure products of the Yokohama Rubber Group used by our customers, and quality issues could lead to losing customers' trust. With this awareness in mind, the Yokohama Rubber Group has defined "customer health and safety" as a critical issue to be addressed, continuously promoting improvement activities.
Our policy and position
Quality Policy
We will contribute to society by planning, designing, producing, and selling attractive products that our customers will be satisfied with while establishing a quality assurance system in all of our processes, including service.
To that end, we will conduct systematic activities in such a way that all the basic steps in our quality assurance activities integrate functionally.
To that end, we will conduct systematic activities in such a way that all the basic steps in our quality assurance activities integrate functionally.
Response to quality-related incidents calls for taking preventive measures, prompt measures to prevent the spread of similar issues, and countermeasures to address the source of issues. In the handling of every quality-related incident, in addition to conducting risk assessments and taking countermeasures that give first priority to the safety of customers, it is necessary to urgently implement measures to prevent the spread of such incidents from the standpoint of recurrence prevention. In order to achieve this, we share all of the processes from the investigation of the root cause of a quality-related incident and the completion of its permanent measures throughout the entire Group, and make company-wide efforts carry out mutual surveillance.
By developing complaint management mechanism, we will enhance our initiatives for the respect of human rights and raise the level of compliance in the entire Yokohama Rubber Group.
By developing complaint management mechanism, we will enhance our initiatives for the respect of human rights and raise the level of compliance in the entire Yokohama Rubber Group.
Impact assessment on product health and safety implemented in each process
Process | Impact assessment on product health and safety |
---|---|
Impact assessment on product health and safety | In plan examinations, we decide on the target quality in new product development based on existing product quality information and forecasts of customer use conditions, and share points to remember concerning product safety with the related departments. |
R&D | Through internally stipulated design reviews, we finalize the means and measures for achieving the target quality described above, confirm conformance with the regulations, standards, and certifications of the destination of shipment, and confirm conformance with the customer’s requirements. We only move on to the mass production process once this has been ensured. |
Manufacturing and production | Legitimacy tests and inspections are conducted to confirm that the target quality has been secured in mass production. The certainty of the effectiveness of our process quality assurance and inspections in each manufacturing process is also maintained through means such as regular internal audits. |
Marketing and advertisements | In order to ensure product safety, we inform customers and business partners of product handling through means such as catalogs and our website. |
Storage and distribution | In order to deliver product quality to customers we monitor the storage and distribution process for the presence of defects so that we can achieve improvement measures. |
Use | We recognize the necessity of explanations and warnings on product use methods, and communicate to spread awareness accordingly. In addition, we endeavor to communicate with customers through customer satisfaction and technology service activities, and we provide feedback to design departments in order to achieve continuous improvements. |
Disposal, reuse, and recycling | We also conduct control for the retread process for truck and bus tires. |
Measures to pursue our vision
In order to further improve the quality activities (PYB management*) we have conducted in the manufacturing process until now, we will enhance frameworks for the development of human resources who can watch over our products released in the market to make sure if their quality has not changed as well as for the prompt communication of such information, and also enhance the internal quality auditing to confirm that such frameworks are functioning properly in a global scale.
- PYB management: A management system to prevent the recurrence of failures that visualizes the implementation status of recurrence prevention measures, in which P (pink) means that a failure has occurred in the manufacturing process, Y (yellow) means remedial measures have been taken, and B (blue) means the effect of such measures have been identified.
Management system
In connection with all important quality-related incident pertaining to products and services provided to customers on a global level, Yokohama Rubber has developed our own risk map to evaluate what kind of impact related failures can have on customers themselves, their household articles, the environment around them, etc., as well as what kind of potential risks such failures can pose, and analyze and classify these risks quantitatively. Based on the results, prompt, legal, and appropriate internal processes that prioritize customer safety are carried out by the Business Division, the Quality Assurance Division and the Service Division. This process is led and monitored by the Quality Audit Department.
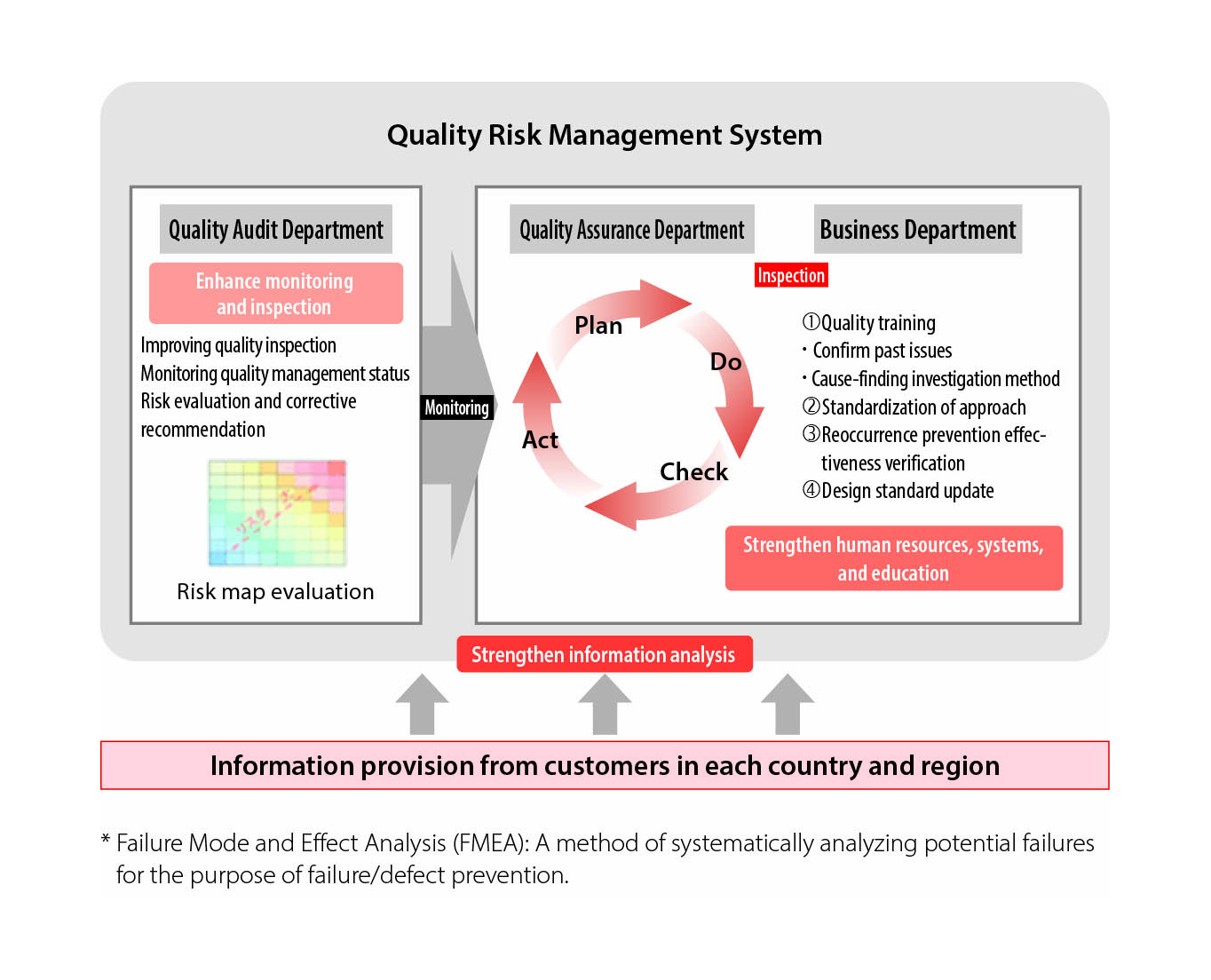
<Response when a problem occurs>
When it is determined that customer safety is not sufficiently ensured, we will implement internal procedures as quickly as possible, take market measures in a legitimate manner, and make that known to our customers through our website and external media.
<Advance prevention and recurrence prevention>
Through the quantitative categorization of potential risks in accordance with a quality management system (QMS) and the introduction of a preventive safety design approach based on FMEA*, we are working to establish a structure that will prevent the recurrence of issues pertaining to similar quality-related matters.
While the phenomenon of quality-related incidents differs depending on the type of business or product, we share cases and countermeasures across the Group because there are many similarities in attitudes toward design approach, risk prediction, environmental consideration, and countermeasures to address the source of issues and prevent their spread broken down by each process even among different type of businesses or products. As part of this effort, we hold a "company-wide quality problem recurrence prevention report meeting" every year for all businesses to examine the measures taken to prevent the recurrence of such incidents and their effectiveness and to confirm how much such information is actually shared across the businesses.
While the phenomenon of quality-related incidents differs depending on the type of business or product, we share cases and countermeasures across the Group because there are many similarities in attitudes toward design approach, risk prediction, environmental consideration, and countermeasures to address the source of issues and prevent their spread broken down by each process even among different type of businesses or products. As part of this effort, we hold a "company-wide quality problem recurrence prevention report meeting" every year for all businesses to examine the measures taken to prevent the recurrence of such incidents and their effectiveness and to confirm how much such information is actually shared across the businesses.
- FMEA(Failure Mode and Effect Analysis): Systematic analysis method to detect potential failures implemented for the purpose of preventing failures and defects
<Human resource development and implementation of seminars for customers>
We appoint experienced engineers at our sales companies and sales sites in the domestic and overseas markets to systematically host in-house training course on product knowledge and their handling. In addition, we make efforts to increase the opportunity to visit our customers in order to hold workshops for them to handle our products safely and properly in a planned manner.
Review of FY 2022 Activities
In FY2022, we continued to enhance our customer consultation service to listen to voices of many more customers.
The number of complaints related to product quality received by the MB Group division decreased by 30% compared to the previous year amid the self-restraint mood caused by the COVID-19 pandemic. The Tire Group, with its scope of coverage expanded, also received complaints related product quality, which marked 17% increase in value terms.
Establishment of a quality assurance system
The basis of quality assurance systems in the automotive industry is conformity with IATF16949. Therefore, we provide quality education and encourage managers and supervisors to acquire the certification of internal quality auditor.
In FY2022, three employees obtained their certification (total number of certified employees: 147).
In addition, to promote the acquisition of high accuracy market information and the rapid response at the occurrence of product failures, the Tire Group has operated a qualification system and formed a service network.
In FY2022, two employees in Japan and 24 overseas were newly certified as tires service engineers. We are now providing training to our employees to be an authorized adjuster to make judgments on complaints.
In FY2022, three employees obtained their certification (total number of certified employees: 147).
In addition, to promote the acquisition of high accuracy market information and the rapid response at the occurrence of product failures, the Tire Group has operated a qualification system and formed a service network.
In FY2022, two employees in Japan and 24 overseas were newly certified as tires service engineers. We are now providing training to our employees to be an authorized adjuster to make judgments on complaints.
<FY 2022>
Move the screen to the left or right to see the table information
Number of staff that has received training and qualifications | In Japan | Overseas |
---|---|---|
Number of staff that obtained IATF 16949 internal auditor certification | 1 in the MB Group (cumulative total of 133) 2 in the Tire Group (cumulative total of 14) |
―― |
Number of staff which was newly certified as a tire service engineer | 2 | 24 |
Total number of certified tire service engineer | 17 | 436 |
Number of the authorized adjusters who can make judgements regarding tire complaints (new) | 0 *The YFS (Yokohama Field Service) certification training could not be held in FY2022, and there were no new certificates. |
0 *We were unable to hold training for delegation of claims adjudication authority for overseas in FY2022, and there were no newly accredited persons. |
Total number of authorized adjusters who can make judgements regarding tire complaints | 778 | 191 |
Introduction of Initiatives
There were two recalls related to tires in FY2022, which were handled appropriately. The MB Group had no recall problems, and did not organize a service campaign.
Future challenges
In order to achieve the eradication of quality issues, and provision of products that clearly address customer needs with safety, legitimacy, and compatibility, we have developed a service network around the world to gather, analyze, and classify the voices of customers and followed the cycle to make sure for such voices to be incorporated into the creation of new products.
In our effort to continue to provide products that will meet customers' needs in their usage environments, we are determined to sincerely accept information about customer complaints and address the challenge of steadily decreasing the number of such complaints. As measures to realize that, we will promote the enhancement of the ability of our service departments to collect market quality information and their market adaptability at each market through contacting our customers through consultation service.
We also face a massive challenge in terms of how to provide quality assurance service with our cooperative companies. We are working on the establishment of a reliable self-check framework based on the clarification of responsibilities and the record of past problems, and the implementation of audit activities for our cooperative companies.
In our effort to continue to provide products that will meet customers' needs in their usage environments, we are determined to sincerely accept information about customer complaints and address the challenge of steadily decreasing the number of such complaints. As measures to realize that, we will promote the enhancement of the ability of our service departments to collect market quality information and their market adaptability at each market through contacting our customers through consultation service.
We also face a massive challenge in terms of how to provide quality assurance service with our cooperative companies. We are working on the establishment of a reliable self-check framework based on the clarification of responsibilities and the record of past problems, and the implementation of audit activities for our cooperative companies.